Testing and Qualification for Extruded DC Transmission Cable Systems
High-capacity extruded DC cable systems have been trending in exporting renewable energy generation such as deep sea wind power, and connecting non-synchronous regional power grids, with the rising demand for clean energy and improved grid reliability. The commercially available extruded DC cable systems for VSC are mainly tested and qualified following CIGRE TB 496 (2012) and IEC 62895: 2017. The prequalification tests specified in those technical documents all comprise long duration voltage test under ± 1.45 U0 followed by superimposed impulse voltage test. The specified type tests comprise electrical tests including load cycle tests under ± 1.85 U0 followed by superimposed impulse voltage test, and non-electrical tests specified in IEC 62067.
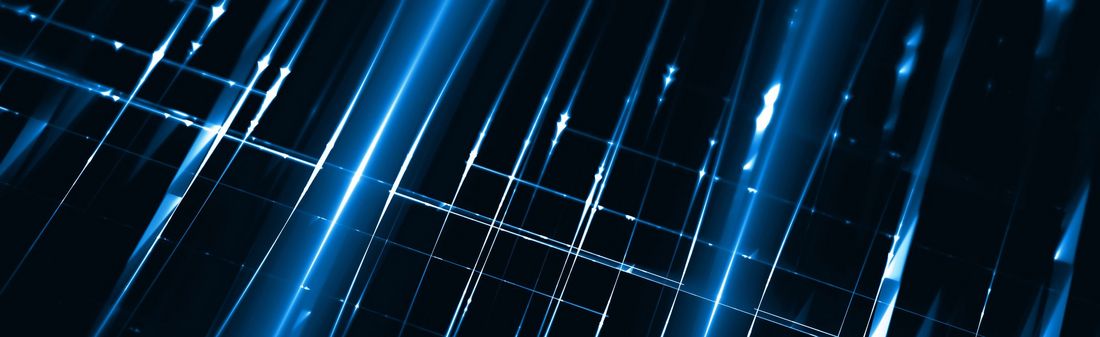
By Xiao Gu, Shanghai National Center of Testing and Inspection for Electric Cable and Wire Co. Ltd. (TICW)
Introduction
While TB 496 provides testing recommendations for DC cable systems up to 500 kV, and IEC 62895 specifies test methods and requirements for DC land cable systems up to 320 kV, the manufacturers and TSOs are motivated to develop extruded DC cable systems above 500 kV, and also to build DC cable systems through complicated route. A land cable system of 640 kV was reported to be qualified in 2017[1], and the 141 km-long commercial transmission submarine cable project of 400 kV has been put into operation since 2019[2]. Despite the updated CIGRE TB 852 (2021) which extended the voltage level to 800 kV and introduced more precise tests such as by-products content measurement and thermal stability test, TSOs and manufacturers have been trying to adopt additional tests to verify the quality of the cable system, as well as to fulfill special requirements raised by the installation and operation of specific projects.
In this article, additional tests designed and carried out to verify the quality of the extruded DC cable systems and to test system performance under peculiar conditions of specific projects are presented for reference.
Additional tests designed for better quality verification
For AC cable systems, the PQ test arrangement shall be representative of different installation design conditions. However, it is recommended to be considered but not compulsory for test arrangement of the PQ test of DC cable systems, as regulated by IEC standard and CIGRE TBs. Sometimes the whole or part of the PQ test loop including terminations can be placed indoors for better temperature control, and the qualified system is acceptable for indoor installation. While in China, PQ tests of extruded DC cable systems are mostly carried out completely in the outdoor environment as required by major TSOs. The terminations and part of the cable shall directly be exposed to all weather conditions for at least a year. The ambient temperature can be ranged from below freezing point to over 40 ℃. For better quality verification, the PQ test arrangement usually consists of installation conditions including direct burial, laid in air, and laid in air-filled pipes. German TSOs also established test arrangement for the 525 kV PQ test including directly buried, arranged in cable protection pipes and tunnel installations, with distributed temperature sensing to monitor the temperature profile of the entire test loop[3]. For submarine cable systems, the repair joint will be placed 1 meter beneath water during the PQ test to check its reliability. After the long-duration voltage test, both the superimposed switching impulse voltage test and the superimposed lightning impulse voltage test will be conducted. By completing the PQ test of such test arrangement and test program, the qualified DC cable system shall be acceptable for indoor and outdoor installation. Figure 1 shows the test setup of the superimposed impulse voltage test for a 400 kV DC submarine cable system during the PQ test, the test arrangement included direct burial, laid in air, laid in air-filled pipes, and the repair joint was placed under water during long duration voltage test.
During the qualification of a 400 kV DC XLPE cable system, additional tests have been conducted for high quality demonstration[2]. Polarity reversal test for the LCC system were successfully conducted as better quality proof, despite that the cable system was designed for a VSC converter system. Load cycle tests with conductor temperature higher than required by the standard were also performed to prove higher quality and stability.
During the prequalification tests of 525 kV land cable and submarine cable systems, the leakage current of the cable system was continuously monitored to evaluate the conductivity of cable insulation with electrical and thermal stresses applied [4]. Full-size space charge measurements on cable insulation via pulsed electro-acoustic method before and after the PQ test were also performed to assess the space charge accumulation brought in by the PQ test and possible insulation aging caused accordingly.
During the qualification process of the ± 400 kV cable system, three factory joints and three land joints were subjected to voltage test followed by a step lightning impulse test, respectively, to test the design margin and uniformity. Each joint sample was firstly subjected to – 400 kV for 2 hours, and then the lightning impulse voltage was raised from + 800 kV to + 2000 kV by several voltage steps [5]. At each voltage level, the impulse voltage was applied to the sample for 10 times. The conductor temperature was maintained no lower than the designed maximum operation temperature during the whole test. The factory joint samples and land joint samples successfully passed the test and proved satisfactory system performance. Figure 2 shows the step lightning impulse test on the factory joint sample after 2 hours of -400 kV DC voltage test.
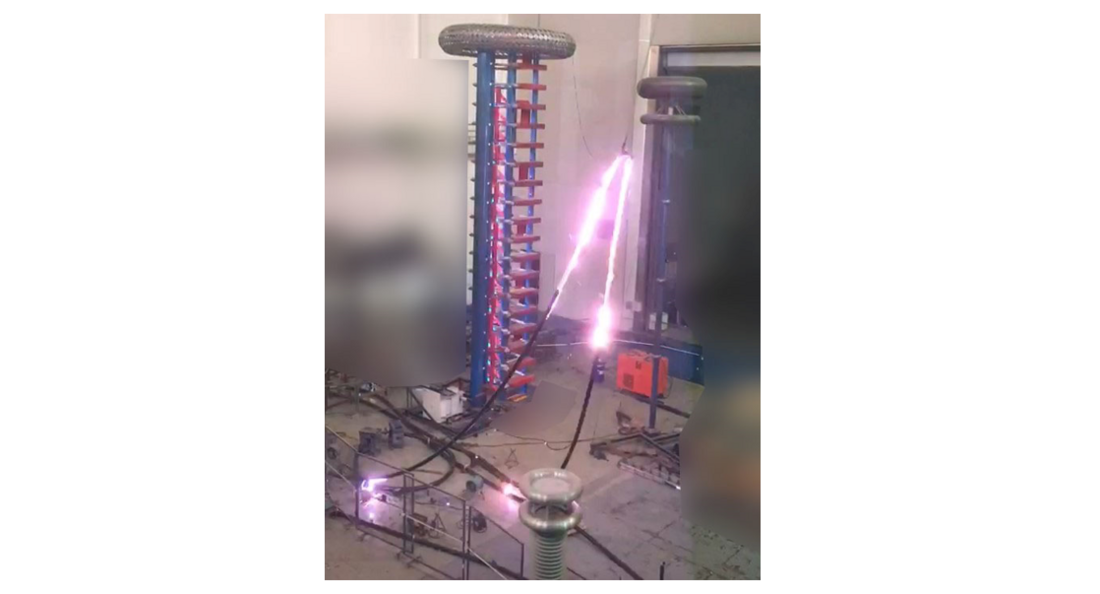
Figure 2 - Photo of step lightning impulse test on pre-energized 400 kV joint sample
In Chinese national standard GB/T 31489 for type test of extruded DC cable systems, void, contaminant, and amber shall be checked for cable insulation and factory joint insulation. Void and protrusion between screens and insulation shall be checked for cable insulation and factory joint. Measurement of space charge in cable insulation slices, and measurement of cable insulation conductivity at different temperatures are also required.
Additional tests designed for specific projects
When qualifying a DC cable system for a specific project, special tests can be designed based on specific installation and operating conditions. For the ± 320 kV interconnection project[6], the land cable system can be exposed to very low temperatures, the superimposed impulse voltage of the PQ test was repeated with a section of the cable cooled down to -25 ℃. The terminations were to be installed where there are pollution conditions, the pollution withstand test under DC voltage was performed after pre-conditioning of eight flashovers under AC.
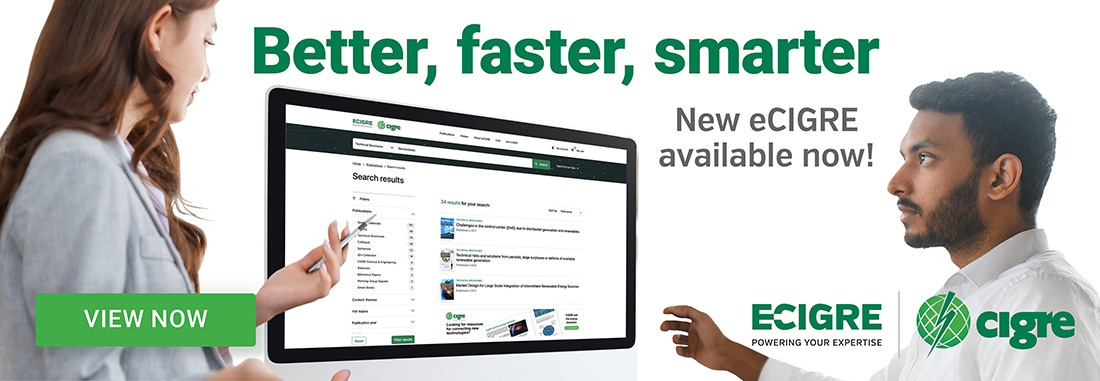
During the qualification of the 400 kV DC submarine cable system for the Rudong project, the TSO requested the superimposed switching impulse test with UP2, S up to ±1235 kV as part of the type test based on the project design, which is tougher than what’s usually required for 500 kV level cable systems. Since the Rudong project operates in symmetric monopole mode, voltage withstand tests were required to be conducted in case of a short circuit fault between the conductor and the earth occurring in one pole. After the electrical type test and before disassembling the test loop, 30-min voltage withstand tests under positive and negative 800 kV at ambient temperature and high temperature were conducted, respectively. The applied voltage was finally raised to + 1000 kV for 5 min to test the design margin. The type test loop successfully passed the additional tests.
Conclusion
Extruded DC cable systems with elevated voltages have been type tested and PQ tested according to the qualification process specified in CIGRE TBs and IEC standard. Additional tests should be developed and performed,
- to verify the cable system quality more thoroughly;
- to test the cable system under complex conditions of specific projects, and test the design margin;
eventually, give more confidence to manufacturers and TSOs.
References
- M. Jeroense, P. Bergelin, et al. ‘Fully qualified 640 kV underground extruded DC cable system’. CIGRE Session 2018, B1-309, Paris.
- T. Igi, S. Asai, S. Mashio, et al. ‘Qualification, installation and commissioning of world’s first DC 400 kV XLPE cable system’. Jicable’ 19, A6-1, Paris.
- A. Braun, J. Bruggmann, et al. ‘PQ test of extruded HVDC 525-kV-underground cables: results and conclusion’. Jicable’ 19, A9-2, Paris.
- S. Hou, Y. Zhao, et al. ‘Experimental practice implemented to improve meaningfulness of prequalification tests for extruded HVDC 525kV land and submarine cables’. ISH 2021, Xi’an.
- X. Gu, Y. Fan, et al. ‘Qualification Process of ±400 kV HVDC Extruded Cable System’. CIGRE Session 2020, B1-214, Paris.
- M. Marzinotto, M. Albertini, L. Benard, et al. ‘Cable system qualification process for the Italy – France HVDC intertie’. CIGRE Session 2016, B1-109, Paris.
Thumbnail credit: Anna Bliokh on iStock