Revêtements destinés à améliorer la performance électrique des isolateurs d'extérieur dans des conditions de pollution
Chef de file
(CA)
M. FARZANEH
Secrétaire
(IT)
A. PIGINI
Secrétaire Assistant
(NO)
B. ADUM
C.C. AMORIM, (BR), N. ARORA (IN), S.A. ASTO SOTO (PE), A. DE CASTRO RIBEIRO (BR), A. DA COSTA (BR), C. CHEMELLI (IT), H. DE SANTOS (ES), A.J. ELIASSON (IS), J. GARCIA (ES), R.W. GARCIA (BR), J.M. GEORGE (FR), P. GRAZIOSI (IT), I. GUTMAN (SE), N. HADINGER(AT), T. HAYASHI (JP), F. JAKL (SI), S. KUEHNEL (DE), J. LAMBRECHT (DE), F. LEHRETZ (DE), L. LI (CN), Q. LI (CN), F. LIRIOS (AU), R. MACEY (ZA), P. MARCACCI (IT), J. MAYA (CO), Y. OKAWA (JP), G. PIROVANO (IT), D. RAMALHO DE MELLO (BR), F. WANG (CN), L.WANG (CN), F. YIN (CN), C. ZIEGLER (AT), R. ZNAIDI (TN)
Contributeurs :
N. ARORA (IN), S.A. ASTO SOTO (PE), A. DE CASTRO RIBEIRO (BR), H. DE SANTOS (ES), M. FARZANEH (CA), J. GARCIA (ES), R.W. GARCIA (BR), J.M. GEORGE (FR), P. GRAZIOSI (IT), I. GUTMAN (SE), R. MACEY (ZA), Y. OKAWA (JP), D. RAMALHO DE MELLO (BR), L. WANG (CN), R. ZNAIDI (TN)
Programme d'activité du Groupe de Travail B2.69 “Revêtements pour équipements des réseaux électriques"
Les dernières décennies ont vu le développement d'une variété de techniques de traitement de surface et de revêtements, apportant des propriétés telles que l'hydrophobicité, l'auto-nettoyage, la protection contre l'accrétion de givre et contre la corrosion. L'industrie de l'électricité peut potentiellement tirer des avantages de ces progrès technologiques, par la réduction des risques de contournement des isolateurs provoqués par la pollution ou le givrage, par la réduction du bruit d'effet couronne des conducteurs, des accessoires de ligne et des isolateurs, par la réduction de la corrosion des éléments métalliques, ainsi que par la réduction des problèmes mécaniques provoqués par le givrage ou l'accrétion de la neige sur les réseaux électriques aériens. Certaines de ces technologies, comme les revêtements antigivre, peuvent non seulement améliorer la fiabilité des installations de transport de l'électricité, mais aussi permettre une réduction des coûts de construction des nouveaux réseaux.
Prenant en compte les considérations précédentes et l'intérêt montré par les parties prenantes pour la recherche de réponses pratiques à ces problèmes par l'utilisation de revêtements, le Groupe de Travail (GT) B2.69 "Revêtements pour équipements de réseau électrique" a été créé en octobre 2017. Le GT constitué de 36 Membres (M) et Membres Correspondants (CM), de 19 pays, a commencé officiellement ses travaux lors de la Session CIGRE de Paris, en août 2018.
Du fait de la multitude des disciplines concernées, de l'étendue du domaine, et des difficultés rencontrées pour identifier et impliquer des membres internationaux possédant une expertise sur tous les sujets à couvrir (pollution, givre, bruit Couronne, corrosion et camouflage), il a été décidé de rassembler les résultats des études dans deux Brochures Techniques (BT), en fonction des expertises et des intérêts de chacun des membres. Ces deux BT sont respectivement : "Revêtements destinés à améliorer la performance électrique des isolateurs d'extérieur dans des conditions de pollution" (BT 837) et "Revêtements de protection des réseaux électriques aériens contre le givre, le bruit de couronne, la corrosion et l'impact visuel" (BT 838). Le présent rapport présente la première BT.
Contenu de la BT “Revêtements destinés à améliorer la performance électrique des isolateurs extérieurs dans des conditions de pollution"
La conception des isolateurs est en grande part déterminée par les niveaux de pollution existants ou anticipés, tout particulièrement pour des environnements sévères de service extérieur, pour lesquelles l'utilisation des isolateurs céramiques sans revêtement (verre ou porcelaine) n'a souvent pas permis d'assurer la tenue et la fiabilité exigées. Les isolateurs avec surface hydrophobique (surfaces constituées de matériau à transfert hydrophobicité (HTM), voir l'exemple Figure 1, présentent une tenue meilleure que les solutions céramiques hydrophiles en terme de tenue de tension dans des conditions de pollution, permettant aussi une éventuelle réduction de la longueur des isolateurs. Le silicone est le produit majoritairement choisi pour conférer à la surface des isolateurs les propriétés HTM requises.
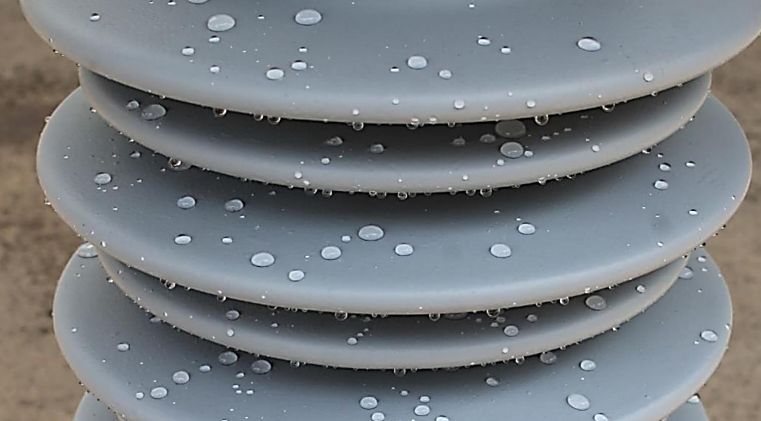
Figure 1 - Exemple d'hydrophobicité d'un isolateur récemment doté d'un revêtement RTV (Vulcanisation à température ambiante)
D'autres matériaux avec des propriétés supérieures, présentant des caractéristiques de super-hydrophobicité, sont toujours en cours d'investigation et ne sont pas encore prêts pour une utilisation en exploitation à grande échelle. Une préoccupation importante qui subsiste concerne la durée de vie attendue de l'isolateur : alors que les isolateurs céramiques constitués de matériaux inorganiques ne sont pas susceptibles de se dégrader fortement avec les années (avec une durée de vie prouvée bien supérieure à 30 ans), les isolateurs présentant des caractéristiques HTM, constitués totalement ou partiellement de matériaux organiques, sont relativement plus susceptibles de connaitre un vieillissement et une dégradation dans la durée, tout particulièrement dans des environnements de service hostiles. Cette dégradation peut se manifester par une perte d'hydrophobicité, des cheminements ou des érosions de surface, qui impactent le comportement électrique.
Différents types d'isolateurs possédant des caractéristiques hydrophobiques sont commercialement disponibles, parmi lesquels des isolateurs composites, des isolateurs hybrides, des isolateurs céramiques graissés, ainsi que des isolateurs céramiques qui ont reçu un revêtement constitué d'une couche fine (de quelques centaines de µm) de caoutchouc silicone vulcanisé à température ambiante (RTV), déposée sur toute la surface de l'isolateur. Ces isolateurs céramiques combinent l'avantage d'une surface possédant des caractéristiques HTM qui apportent des possibilités accrues de tenue de tension dans des conditions de pollutions, et la robustesse et la tenue mécanique bien reconnues de la céramique.
Les premières applications des revêtements de silicone RTV ont en majorité été réalisées sur site, et ont été considérées comme des solutions palliatives, destinées à réduire les contournements d'isolateurs et de traversées dont le comportement en exploitation était défectueux (Figure 2).
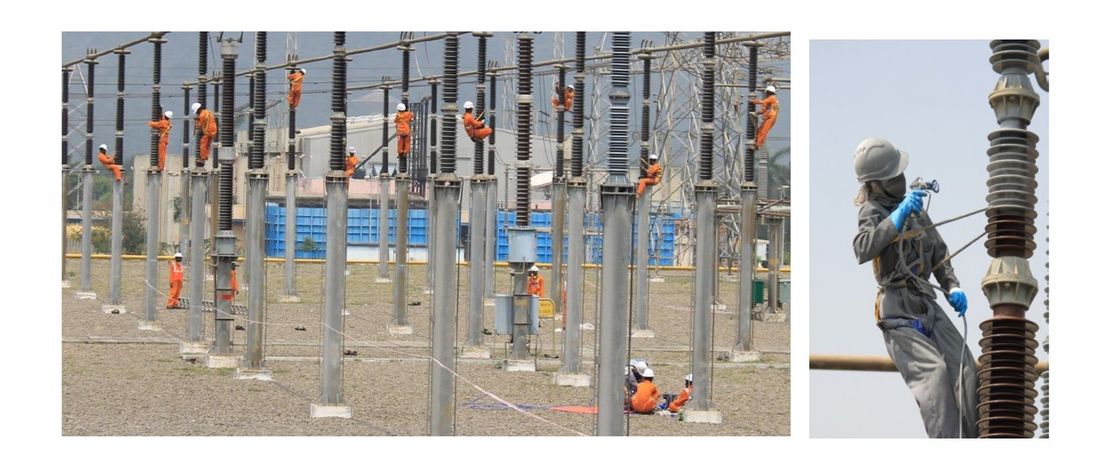
Figure 2 – Revêtement d'isolateurs de poste : nettoyage d'isolateur et application de revêtement
Au cours de la dernière décennie on a vu une envolée du choix d'isolateurs dont le revêtement a été réalisé en usine, tout particulièrement pour les isolateurs à capot et tige (Figure 3). Les isolateurs pré-revêtus sont aujourd'hui considérés comme la solution viable à adopter dès la phase de conception. On estime qu'environ 10 millions d'unités d'isolateurs à capot et tige revêtus sont en service en 2020, et si on poursuit selon la même tendance, l'extrapolation des données conduit à une multiplication par 10 sur dix ans, c’est-à-dire qu'il y en aura 100 millions en service en 2030. Les projections de marché concernant le revêtement des isolateurs des postes sont également robustes, mais à une échelle moindre que pour les lignes de transport. Alors que beaucoup des compagnies d'électricité voient le revêtement des isolateurs de poste comme une mesure palliative, certaines d'entre elles, de par le monde, demandent l'adoption du revêtement des isolateurs de poste dès le stade de la conception. Dans l'Annexe de la BT on présente l'évolution et les tendances en matière de recours au revêtement RTV dans différents pays.
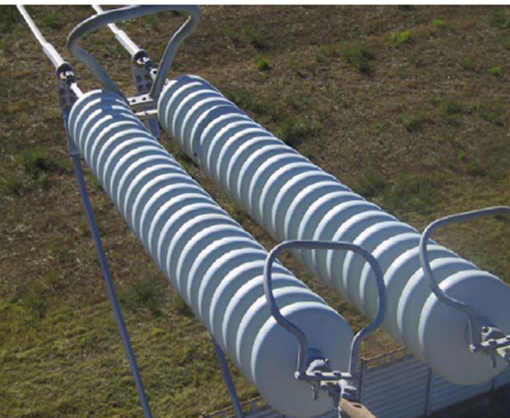
Figure 3 – Chaîne d'ancrage 380 kV équipée d'isolateurs à capot et tige pré-revêtus de RTV
Etant donné la croissance globale, réalisée et anticipée, de l'utilisation des revêtements RTV, il émerge un besoin pressant de normes qui spécifient, et évaluent, la qualité du revêtement RTV et des isolateurs traités. Il n'existe pas de norme CEI pour le moment et il est prévu qu'une annexe d'information soit incluse dans la révision en cours de la norme CEI 60383-1 traitant des isolateurs de ligne. Les spécifications des utilisateurs sont le plus souvent dérivées d'une combinaison de BT CIGRE anciennes (BT 478 et BT 595), de directives IEEE, de diverses normes nationales et d'essais adaptés, quand c'est nécessaire, de normes CEI existantes traitant d'autres produits (par ex. des isolateurs composites ou des isolateurs hybrides). Dans l'objectif de contribuer à une future normalisation CEI, on a analysé en détail dans la BT les essais proposés ou adoptés trouvés dans différentes spécifications de constructeur et de client, en distinguant les essais de matériaux RTV et les essais des isolateurs revêtus. On décrit les essais de caractérisation des matériaux RTV aux plans physique et électrique, en portant une attention spéciale pour évaluer "l'empreinte" du matériau et son hydrophobicité, ainsi que sa tenue en matière de cheminement et d'érosion. Quant aux isolateurs traités, les différents essais proposés pour évaluer leur hydrophobicité, l'adhérence du revêtement, la tenue de la tension en conditions de pollution, et leur comportement sur le long terme, sont analysés, en mettant en exergue les aspects appelant des investigations complémentaires. En ce qui concerne le comportement sur le long terme, on insiste sur la pertinence des essais de vieillissement des isolateurs réalisés dans des stations d'essai "naturelles", situées dans des emplacements représentatifs des environnements sévères.
En ce qui concerne la procédure de revêtement, les instructions données dans la BT synthétisent plus de 30 années d'expérience de divers constructeurs, prestataires de service et utilisateurs. On examine les applications sur les isolateurs en service et en usine (pour les isolateurs pré-revêtus), ainsi les différentes procédures d'application du revêtement (brossage, pulvérisation et trempage), les possibilités d'automatisation, et les exigences de contrôle de qualité. Surtout pour le cas des isolateurs de ligne, il est souligné qu'une meilleure qualité du revêtement est en général obtenue avec les processus de revêtement en usine, en comparaison du résultat du revêtement sur site/ en exploitation, et qu'il faudrait retenir l'option à chaque fois que c'est possible et viable. Pour éviter les dommages au revêtement, on aborde aussi dans la BT les questions d'emballage et de manutention des isolateurs traités.
Les aspects de durée de vie sont abordés et on conclut qu'il n'est pas possible d'avoir des indications sur la durée de vie attendue d'un revêtement RTV (et par conséquent de prolonger les assurances et garanties génériques). Le vieillissement et l'espérance de vie sont étroitement liés à plusieurs facteurs, parmi lesquels, sans prétendre être exhaustif, la formulation du matériau RTV spécifique et ses caractéristiques, la géométrie de l'isolateur et son dimensionnement, la qualité de l'application et les contraintes de l'environnement. Le retour d'expérience d'exploitation permet d'avancer que la durée de vie du revêtement peut aller de quelques années à plus de 20 années. Des recherches complémentaires sont requises pour confirmer la pertinence et l'impact de chacun des facteurs qui contribuent au processus de vieillissement, mais la longueur de la ligne de fuite spécifique de l'isolateur influe sur la longévité, et ce point est également discuté.
Différentes méthodes de diagnostic permettant d'évaluer l'état du revêtement en exploitation sont analysées, ainsi que les procédures de maintenance. Bien que les revêtements RTV ne requièrent pas habituellement de lavage, cette option reste possible dans des cas d'utilisation dans des conditions exceptionnellement sévères. La réfection du revêtement peut aussi être envisagée dans certains scénarios, si elle est économiquement viable et praticable.
Finalement, des suggestions des spécifications de revêtement sont résumées et des exemples de spécifications aujourd'hui adoptées pour des isolateurs revêtus sont analysés, confirmant l'urgent besoin d'une norme CEI de référence.