Coatings for improvement of electrical performance of outdoor insulators under pollution conditions
Convenor
(CA)
M. FARZANEH
Secretary
(IT)
A. PIGINI
Assistant Secretary
(NO)
B. ADUM
C.C. AMORIM, (BR), N. ARORA (IN), S.A. ASTO SOTO (PE), A. DE CASTRO RIBEIRO (BR), A. DA COSTA (BR), C. CHEMELLI (IT), H. DE SANTOS (ES), A.J. ELIASSON (IS), J. GARCIA (ES), R.W. GARCIA (BR), J.M. GEORGE (FR), P. GRAZIOSI (IT), I. GUTMAN (SE), N. HADINGER(AT), T. HAYASHI (JP), F. JAKL (SI), S. KUEHNEL (DE), J. LAMBRECHT (DE), F. LEHRETZ (DE), L. LI (CN), Q. LI (CN), F. LIRIOS (AU), R. MACEY (ZA), P. MARCACCI (IT), J. MAYA (CO), Y. OKAWA (JP), G. PIROVANO (IT), D. RAMALHO DE MELLO (BR), F. WANG (CN), L.WANG (CN), F. YIN (CN), C. ZIEGLER (AT), R. ZNAIDI (TN)
Contributors:
N. ARORA (IN), S.A. ASTO SOTO (PE), A. DE CASTRO RIBEIRO (BR), H. DE SANTOS (ES), M. FARZANEH (CA), J. GARCIA (ES), R.W. GARCIA (BR), J.M. GEORGE (FR), P. GRAZIOSI (IT), I. GUTMAN (SE), R. MACEY (ZA), Y. OKAWA (JP), D. RAMALHO DE MELLO (BR), L. WANG (CN), R. ZNAIDI (TN)
WG B2.69 “Coatings for power network equipment” activity summary
The last decades saw the development of a variety of surface engineering techniques and advanced coatings with properties like hydrophobicity, self-cleaning, icephobicity and anti-corrosion. These technological advances can potentially benefit the power industry in reducing the risk of insulator flashover due to pollution and icing, corona noise from conductors, fittings and insulators, corrosion of metal elements, as well as mechanical problems caused by ice and snow accretion on overhead power networks. Some of these technologies such as icephobic coatings not only have the potential to increase the reliability of transmission assets, but may also enable a reduction in the capital cost of new power network constructions.
In view of the above concerns and the great interest shown by the stakeholders in finding practical solutions to these problems through the application of coatings, WG B2.69 titled "Coatings for power network equipment", was created in October 2017. The Group, with 36 members (M) and corresponding members (CM) from 19 countries, officially started its work during the Paris session in August 2018.
Given the multidisciplinary and breadth of the topic and the difficulty of identifying and involving international members with expertise in all the subjects concerned (pollution, icing, corona noise, corrosion and camouflage), it was decided to present two Technical Brochures, taking into account the expertise and interest of each member. The titles of the Technical Brochures are as follows:
- TB 837 - Coatings for improvement of electrical performance of outdoor insulators under pollution conditions;
- TB 838 - Coatings for protecting power network equipment against icing, corona noise, corrosion and visual impact.
The present report deals with the first topic.
“Coatings for improvement of electrical performance of outdoor insulators under pollution conditions” summary
Insulator design is largely determined by existing and foreseen pollution levels, especially in harsh outdoor service environments where the deployment of uncoated ceramic insulators (glass and porcelain) has been often incapable of assuring the required performance and reliability. Insulators with hydrophobic surfaces (surfaces made of Hydrophobicity Transfer Materials: HTMs), see example in Figure 1, perform better than ceramic hydrophilic solutions in terms of withstand voltage under pollution conditions, also allowing possible reduction in the required insulator length. Silicone is the prevalent product of choice to lend an insulator surface the requisite HTM properties.
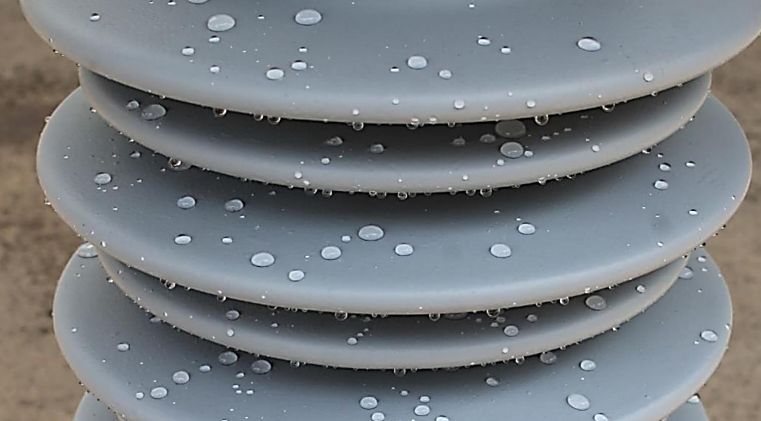
Figure 1 - Example of hydrophobicity on newly RTV (Room Temperature Vulcanizing) coated insulator
Other materials with enhanced performance displaying superhydrophobic characteristics are still under investigation and are not yet ready for wider field adoption. A key consideration that persists is insulator expected life: while ceramic insulators made of inorganic materials are not prone to appreciable degradation with age (with a proven life of well above 30 years), insulators with HTM characteristics made, fully or partially, of organic materials are relatively more prone to ageing and degradation while ageing, especially under hostile service environments. This degradation may manifest as a loss of hydrophobicity, surface tracking and erosion that impact electrical performance.
Different types of insulators with hydrophobic characteristics are commercially available, including composite insulators, hybrid insulators, ceramic greased insulators as well as coated-ceramic insulators obtained by uniformly applying a thin layer (a few hundred µm) of silicone RTV (Room Temperature Vulcanizing) rubber all along the insulator surface. Coated ceramic insulators offer the combined advantage of a surface with HTM characteristics that provides a vastly improved withstand voltage capability under pollution conditions coupled with the well-established mechanical robustness and strength of the underlying ceramic.
Most earlier applications of RTV silicone coatings were conducted on-site and were considered a remedial measure to mitigate pollution flashovers on insulators and bushings that demonstrated poor service performance in the field.
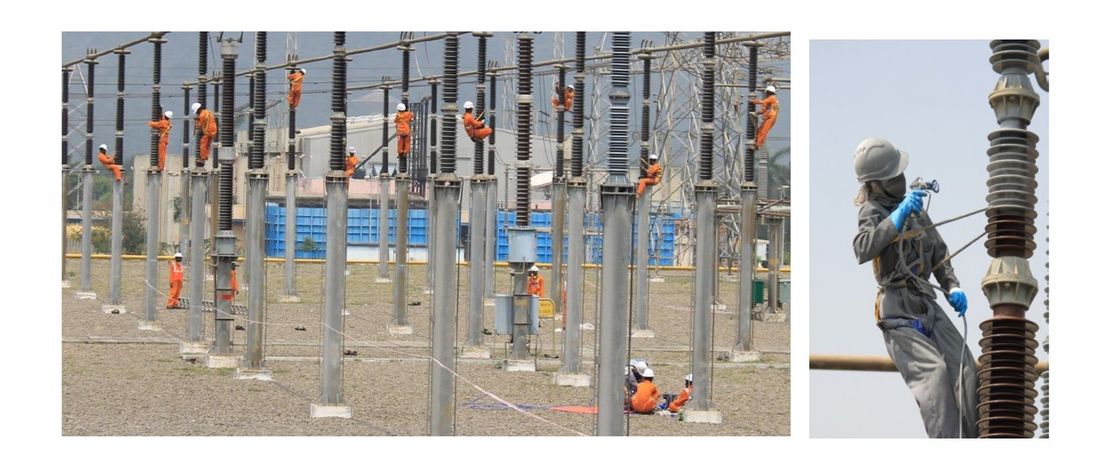
Figure 2 - Station insulators coating: insulator cleaning and coating application
Over the past decade there has been a spurt in the adoption of factory-coated insulators, especially for cap and pin insulators. Pre-coated insulators are now considered as one of the viable solutions to be adopted during the design phase itself. About 10 million coated cap and pin insulator units are estimated to be in use in 2020 and, continuing with this evolution trend, extrapolated data indicates a 10x growth so that the number of such pre-coated insulators in the field may reach 100 million in 2030. Market projections for RTV coating of station insulators is also robust, although not at the same scale as for transmission lines. While many utilities continue to view coating of station insulators as remedial measure, some utilities worldwide are mandating the use of coating on station insulators at the design stage itself. Evolution and trends of the application of RTV coating in the different countries are stated in the Appendix.
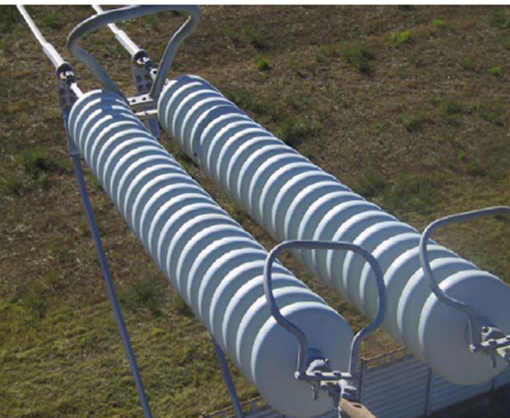
Figure 3 - 380 kV anchor string equipped with pre-coated RTV cap and pin insulators
Given the realized and expected growth of RTV coating globally, there is a pressing need for standards to specify and assess the quality of RTV coating and of coated insulators. There is no IEC Standard as yet and an informative annex is foreseen to be included in the ongoing revision of IEC 60383-1 Standard dealing with line insulators. User specifications are most often derived from a combination of previous CIGRÉ Technical Brochures (TB 478 and TB 595), IEEE guidelines, various national standards and adapted tests, as necessary, from existing IEC Standards for other products (e.g., composite insulators or hybrid insulators). With the intention to contribute towards future IEC Standardization, tests proposed and/or adopted in various manufacturer and customer specifications are analysed in detail in this TB, subdividing them into tests for RTV material and tests for coated insulators. Tests to characterize the RTV material from the physical and electrical point of view are described, with special attention to tests necessary to assess material “fingerprinting” and its hydrophobicity and performance from the point of view of tracking and erosion. For coated insulators the various tests proposed to assess hydrophobicity, coating adhesion, withstand voltage under pollution condition and expected long-term performance are analysed, pointing out aspects needing additional investigation. As far as long-term performance, the relevance of ageing tests at natural insulator test stations located in areas representative of harsh environments is stressed.
As far as coating procedure is concerned, guidelines herein summarize more than 30 years of experience of various manufacturers, service providers and users. In-situ and factory applications (pre-coated insulator applications) are examined, as are various application procedures (brushing, spraying and dipping), automation possibilities and quality control requirements. With special reference to line insulators, it is pointed out that better coating quality may generally be obtained by factory coating processes as compared to on-site/in-the-field coating and should be opted for whenever possible and viable. Packaging and handling of coated insulators to prevent damage to insulator coating are also covered herein.
Considerations on life expectancy are reported concluding that it is not possible to predict indications on the expected service life of an RTV coating (and consequently, to extend generic warranties and guarantees). Ageing and life expectancy are closely linked to several factors including but not limited to the specific RTV material formulation and characteristics, insulator geometry and sizing, application quality and environmental stresses. Based on field experience, coating life may extend from a few years to more than 20 years. While additional research is necessary to ascertain the relevance and impact of each contributory factor in the ageing process, the role of specific creepage distance on longevity is also discussed.
Various diagnostic methods to assess coating conditions in service are analysed. Maintenance procedures are also examined. Although RTV coatings do not usually require washing, the option is available for use in exceptionally harsh conditions. Recoating may also be considered in some scenarios, if economically viable and practical.
Finally, suggestions for coating specification are summarized and examples of specifications presently adopted for coated insulators are analysed, confirming the urgent need of a reference IEC standard.