Coatings for protecting overhead power networks against icing, corona noise, corrosion and reducing their visual impact
Convenor
(CA)
M. FARZANEH
Secretary
(IT)
A. PIGINI
Assistant Secretary
(NO)
B. ADUM
C.C. AMORIM, (BR), N. ARORA (IN), S.A. ASTO SOTO (PE), A. DE CASTRO RIBEIRO (BR), A. DA COSTA (BR), C. CHEMELLI (IT), H. DE SANTOS (ES), A.J. ELIASSON (IS), J. GARCIA (ES), R.W. GARCIA (BR), J.M. GEORGE (FR), P. GRAZIOSI (IT), I. GUTMAN (SE), N. HADINGER(AT), T. HAYASHI (JP), F. JAKL (SI), S. KUEHNEL (DE), J. LAMBRECHT (DE), F. LEHRETZ (DE), L. LI (CN), Q. LI (CN), F. LIRIOS (AU), R. MACEY (ZA), P. MARCACCI (IT), J. MAYA (CO), Y. OKAWA (JP), G. PIROVANO (IT), D. RAMALHO DE MELLO (BR), F. WANG (CN), L.WANG (CN), F. YIN (CN), C. ZIEGLER (AT), R. ZNAIDI (TN)
Contributors:
C.C. AMORIM (BR), N. ARORA (IN), S.A. ASTO SOTO (PE), C. CHEMELLI (IT), A.J, ELIASSON (IS), M. FARZANEH (CA), J.M. GEORGE (FR), N. HADINGER (AT), F. JAKL (SI), Q. LI (CN), F. LIRIOS (AU), P. MARCACCI (IT), J. MAYA (CO), Y. OKAWA (JP), G. PIROVANO (IT), F. WANG (CN), F. YIN (CN), C. ZIEGLER (AT)
WG B2.69 “Coatings for power network equipment” activity summary
The last decades saw the development of a variety of surface engineering techniques and advanced coatings with properties like hydrophobicity, self-cleaning, icephobicity and anti-corrosion. These technological advances can potentially benefit the power industry in reducing the risk of flashovers on polluted and ice-covered insulators, corona noise from conductors, fittings and insulators, corrosion of metal elements, as well as mechanical problems caused by ice and snow accretion on overhead power networks. Some of these technologies such as icephobic coatings not only have the potential to increase the reliability of transmission assets but may also enable a reduction in the capital cost of new power network constructions.
In view of the above concerns and the great interest shown by the stakeholders in finding practical solutions to these problems through the application of coatings, WG B2.69, titled "Coatings for power network equipment", was created in October 2017. The Group, with 36 members (M) and corresponding members (CM) from 19 countries, officially started its work during the Paris session in August 2018.
Given the multidisciplinary and breadth of the topic and the difficulty of identifying and involving international members with expertise in all the subjects concerned (pollution, icing, corona noise, corrosion and camouflage), it was decided to present two Technical Brochures, taking into account the expertise and interest of each member. The titles of the Technical Brochures are as follows:
- TB 837 - Coatings for improvement of electrical performance of outdoor insulators under pollution conditions;
- TB 838 - Coatings for protecting overhead power networks against icing, corona noise, corrosion and reducing their visual impact.
The present report deals with the second topic.
Coatings for protecting overhead power networks against icing, corona noise, corrosion and reducing their visual impact
The main purpose consists of identification of new practical and durable coatings as well as surface engineering techniques in order to increase the reliability of overhead power network equipment in various environmental conditions. It also addresses some environmental concerns caused by corona noise and visual aspects of overhead power lines. The main power network features considered are insulators, conductors and ground wires, and transmission line structures.
The following coatings are considered in this TB:
- Anti-icing: conductors, ground wires, insulators
- Anti-noise: conductors and fittings
- Anti-corrosion: metal parts
- Camouflage: general appearance of the line
In order to identify and examine existing coatings and their potential advantages for use in overhead power network equipment for improved reliability under different environmental conditions, a review of the most relevant coatings was carried out. In addition, characterization of coatings, application methods as well as the need for future R&D studies were discussed.
Anti-icing coatings
Anti-icing coatings are designed to prevent or reduce the accumulation of ice and snow on power network equipment. After a reminder of certain fundamental aspects of icing, a review of developed coatings including concepts, materials typology, elaboration and application methods is carried out and the test methods for characterizing the performance of these coatings are described.
A review of some of the existing passive coatings that can be applied to conductors, ground wires, and outdoor insulators shows that commercial products for application on conductors and ground wires are still lacking. Regarding active coatings, existing concepts such as those based on the electrolysis of ice and the injection of a pulsed current into a conductive coating on a conductors or ground wires are inefficient or impractical. One of the effective active methods developed is based on the use of a ferromagnetic coating for melting wet snow. However, applying this technique to melting ice would require additional R&D efforts.
Regarding outdoor insulators, some coatings such as RTV (Room Temperature Vulcanizing) silicone have already been widely used primarily to reduce pollution flashovers. However, the application of RTV coatings to outdoor insulators in icing conditions is not recommended. Several anti-icing coatings intended to prevent icing flashovers have also been developed and tested. However, these coatings are not yet ready for applications due to their unsatisfactory stability and durability. Further R&D efforts are needed to find efficient and cost-effective techniques to protect insulators under icing conditions.
Finally, to test and characterize the performance and durability of anti-icing coatings, several methods, in the absence of appropriate standards, which have been adopted in different laboratories, have been presented and discussed. Although a number of these methods, with some modifications, can be applied for testing these coatings, refinement of some of these techniques, as well as the development of new methods, is required.
Anti-noise coatings
The audible noise emitted from high voltage transmission lines is usually caused by corona discharge in the highly stressed regions near the conductors, insulators and fittings (Fig. 1). This can lead to the release of a sound perceived as noise by humans.
The main purpose of this chapter is to carry out a comprehensive review of the literature relating to audible noise associated with corona discharge from high voltage transmission lines, especially conductors and insulators in wet conditions. This review also includes measurement methods of audible noise and attenuation options based on surface treatment and coating application.
Regarding the reduction of the corona noise emitted by conductors, it is possible to minimize the surface voltage gradient of the conductors by using large diameter conductors or by using bundled conductors at the design stage of a line. However, for existing lines, corona audible noise, which can be intense in adverse weather conditions (rain, high humidity, etc.), can be reduced by sandblasting or bead blasting of the conductor surfaces. Another possibility is the application of a hydrophilic coating which can in certain cases give comparable or even better results than bead blasting. It should be noted that the treatments mentioned for existing lines are also applicable to new conductors at the manufacturing stage. For insulators, RTV silicone coatings appear to be effective in reducing the audible noise of polluted insulators.
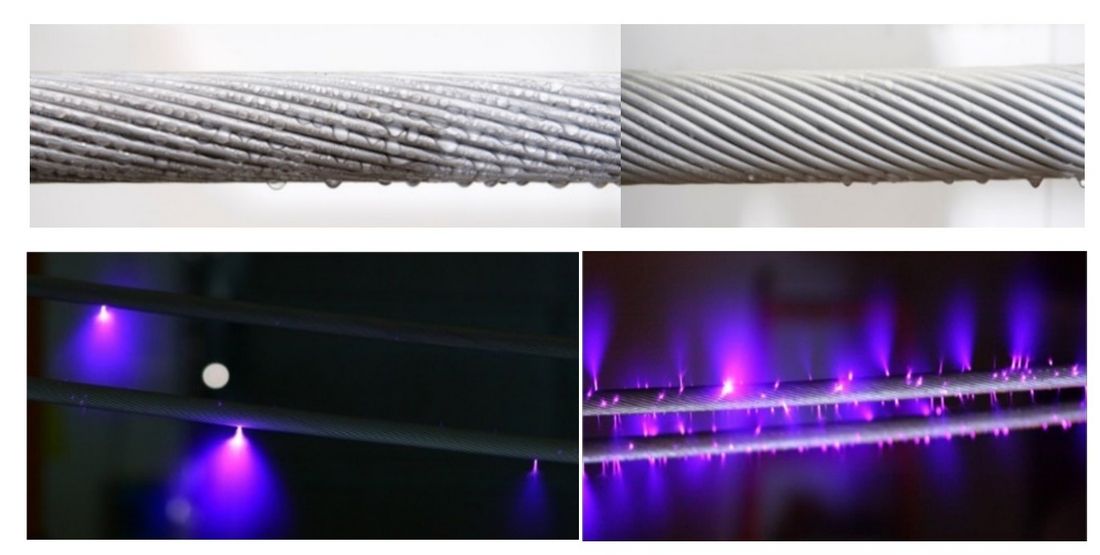
Figure 1 - Surface treatment to reduce the corona and associated audible noise with a hydrophilic surface (left pictures)
Further investigations are needed to improve techniques based on surface engineering and hydrophilic coatings to minimize the emission of corona audible noise from transmission line conductors in adverse weather.
Anti-corrosion coatings
In power networks, many economic losses are linked to the corrosion of line sections located in coastal and/or industrial areas. In fact, marine and industrial pollutants cause corrosion on metal components, such as conductors (Fig. 2), fittings, insulator electrodes and support structures. The main objective of this chapter is to present in detail the methodology adopted by public services confronted with this problem. It also aims to present techniques used to prevent or mitigate the effects of corrosion.
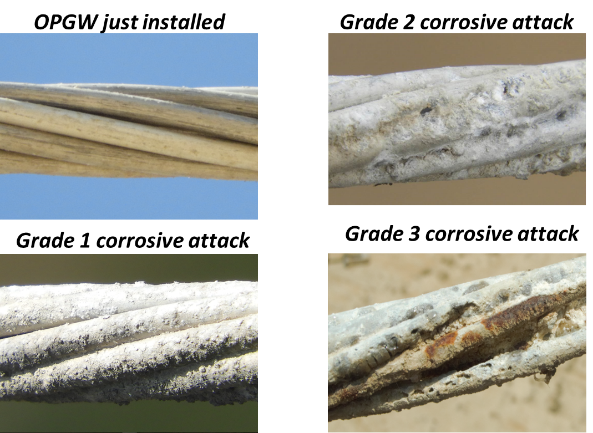
Figure 2 - Photographic patterns used for the evaluation of the OPGW (optical ground wire) without grease or coating in areas of high corrosive aggressiveness
The durability of a corrosion protection system for galvanized steel and aluminium alloys, from which many components of power network equipment are manufactured, is influenced by the corrosivity of the concerned environment. Durability is determined as the expected life of the corrosion protection system until the time of the first major maintenance. Based on the literature review and field experiences, there are several practical techniques for evaluating natural corrosion processes. The key point is the correct and timely diagnosis to find and use the most effective technique to protect all key equipment against corrosion. The choice of a coating and its application to a piece of equipment is highly dependent on environmental parameters and the equipment to be protected.
Field testing of a coating as proposed in this chapter is the most appropriate method for evaluating its performance even though such evaluation usually takes several years. Furthermore, some products may be useful in some environs and conditions but not in others. Factors such as rain, sand or salinity are decisive parameters in this regard.
Although most of the existing anticorrosive coatings are commonly used by electric utility companies, further R&D efforts are needed to develop more effective and durable coatings for use in highly corrosive environments.
Camouflage coatings
Reducing the visual impact of overhead power lines and associated towers and poles by means of camouflage to gain public support and statutory approval has become an increasingly popular option in recent years.
Beginning in the 1980s, several manufacturers of conductors, ground wires, fittings and insulators for overhead power lines began to develop proprietary colouring processes for their products. At the same time, construction companies began to acquire know-how on how to string coloured conductors and use coloured equipment or painted towers, fittings and insulators. Over the past thirty years, the handling and processes of colouring products have been optimized and quality has improved
The main objective of this chapter is to present methods to reduce the visual impact of an overhead line.
The technique used for camouflage of towers and poles is painting hot-dip galvanized structure components using suitable pigments. Coating planning should be done in the production phase. Fittings are also mostly painted but powder coating has been applied more often in recent years. Regarding the camouflage of conductors, two main technologies, namely the application of varnishes and coatings by an electrochemical process, have been used with success. For the camouflage of insulators, the current technique consists in applying an RTV silicone coating using the same procedures as those used for pollution mitigation. Camouflaged insulators are mainly used in new lines or those to be completely or significantly refurbished. The prevalent coating application process today is a factory coated application.
The application of camouflage should be considered in the planning phase of the project as this increases the material cost. Application of the coating is preferred in the factory unless this is done as refurbishment, in which case on-site application is the only economic option.
By implementing all or parts of the measures mentioned, the visibility of a power line can be considerably reduced (Fig. 3). However, it is evident that the colour of the tower background can and will change with the season, the point from which the power line is seen or the angle of solar incidence. Therefore, the visibility of the line could be very low at one time of the year, while high at another

Figure 3 - Comparison between (not visible) black coated conductors and conductors with no surface finis