Life cycle testing of synchrophasor based systems used for protection, monitoring and control
Synchrophasor systems constitute a suite of different system solutions aimed at meeting various wide-area application requirements. What characterizes the synchrophasor systems that is not common to any other measurement infrastructure used in the power grid is the following:
• The design has high sensitivity to the accuracy of the clock (time) reference supplied through either a physical GPS/GNSS receiver placed in the substation next to the IED or a “virtual GPS/GNSS receiver” located remotely from the substation.
• The end-to-end solutions are typically implemented using hardware/software components acquired from multiple vendors. Hence there is a need for consistency in performance across products from different vendors.
• The solutions are quite often used across different personnel groups within a given utility company, as well as across different enterprises such as transmission system operator (TSO) and independent system operator (ISO). This may require consistent life cycle management policies across multiple legal entities (enterprises) and perhaps Federal/state jurisdictions.
Convenor
(US)
M. KEZUNOVIC
N. ANTII-JUHANI (FL), R. BHARAT (AU), M. GREENWOOD (NL), Y. LIU (US), D.V.S. STEARN (GB)
CORRESPONDING MEMBERS: T. BI (CN), D. DUBININ (RU), H. LIU (CN), R. FERNANDES (BR)
CONTRIBUTOR: M. KEZUNOVIC (US)
The end-to-end data flow in a typical synchrophasor solution is shown in Figure 1.
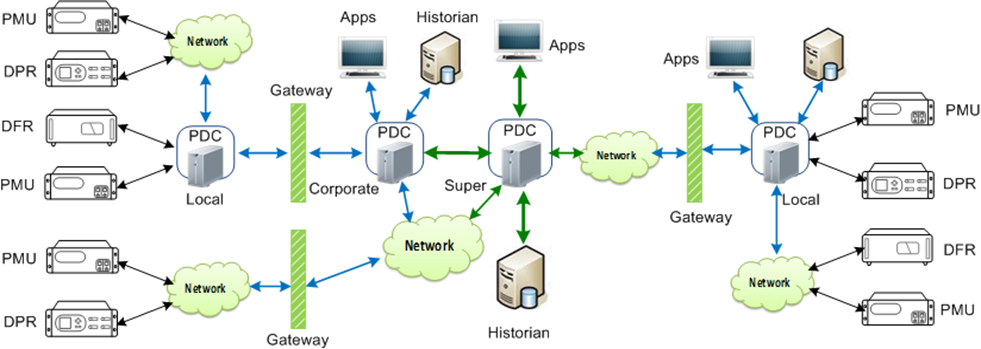
Figure 1 - Typical Phasor Measurement Device Architecture with PDCs at different levels
From the figure, one may observe that the solutions consist of many diverse parts: Phasor Measurement IEDs (PMU, DPR, DFR, etc.), Phasor Data Concentrators (PDCs), and many communication, data management and visualization servers acting as gateways, data historians, and data analytics engines. To ensure the system meets interoperability requirements, one has to anticipate how the future expansion of the system may unfold. The synchrophasor systems are rather complex and require appropriate life cycle management that not only focuses on individual devices such as PMUs and PDCs but also on end-to-end system solutions comprising many devices and communication requirements.
Discussion
The brochure first addresses the issues of synchrophasor system definition and possible architectures. The key conclusion is that synchrophasor systems may consist of many components such as phasor measurement units (PMUs), phasor data concentrators (PDCs), as well as time-precision signal receivers and communication systems making them a very complex system to commission, test and maintain. Due to their importance, it is emphasized that such systems need to be carefully tested for compliance with standards, and then properly deployed through commissioning tests, and eventually tested periodically when expansions are made or they miss-operate.
Next, the relevant standards that apply to the topic of synchrophasors are discussed. The standards are mainly developed by IEEE and IEC, but some national standards are developed to ensure specific requirement relevant to a given country, such as China. A brief summary is discussed next.
IEEE C37.118.1-2011 and its amendment IEEE C37.118.1a-2014 “IEEE Standard for Synchrophasor Measurements for Power Systems” provide basic accuracy requirements as well as time response requirements for a synchrophasor measurement to made by a Phasor Measurement Unit. The main concept defined in 1995 has basically stayed the same, measurements need to be within 1% Total Vector Error (TVE). Adjustments have been made for frequency and Rate of Change of Frequency (ROCOF).
The IEEE C37.118.1-2011 standard has been revised in 2014 to relieve some of the performance requirements, as it was found that after publishing the original standard, some of the requirements could not be met by the proposed reference algorithm. It was noted that full conformance to C37.118.1-2011 is therefore not possible using the reference algorithm, and reference should hence always be made towards IEEE C37.118.1a-2014.
In 2018 the latest revision to C37.118.1 had been finished. This revision includes an optional extension to the 1% TVE requirement. Manufacturers can now specify accuracy for Phase as well as for Magnitude separately. This optional extension can be very helpful for specifying PMUs that require higher than 1% TVE accuracy for certain applications. Another option given to manufacturers is to claim conformance at a certain report rate, therefore limiting the need to perform and test at all possible report rates. The published standard is a so-called “dual logo” standard with IEC. The published standard is titled IEEE 60255-118-1-2018, or IEC/IEEE 60255-118-1 Edition 1.0 2018-12. It is also mentioned that IEEE offers a Conformity Assessment Program (ICAP) for IEEE C37.118.1-2011 as well as IEEE C37.118.1a-2014. The IEEE offers a separate program for IEC/IEEE 61850-9-3:2016. These programs have selected labs that carry out testing on PMUs as well as timing products to ensure conformance to these standards.
It was noted that the IEEE also introduced a Guide for Synchronization, Calibration, Testing, and Installation of Phasor Measurement Units, this is IEEE C37.242-2013. This standard can be used as a reference document for implementing PMUs in a Wide Area Measurement System (WAMS). It is due for revision, so a revised version will be published in 2021 and should be used as a supplemental reading.
The brochure discusses the integration requirements next. It is recognized that there is a need to integrate equipment from different manufacturers into a completed system. The individual pieces of equipment must be able to communicate with each other using common standards – this is referred to as interoperability. This is different from Interchangeability, in which any component can be swapped out with another component without affecting the functionality of the overall system. When two or more pieces of equipment are interoperable, is it possible to integrate them together, but some engineering effort will be required in order to ensure that they work correctly together. These concepts are particularly important for synchrophasors because these signals can be produced by a multitude of different types of devices, from stand-alone units to protection relays or dedicated fault recorders.
Based on the status in the industry, most of the testing, including calibration and type testing, is done in the early stages during the acceptance step. The effort is performed by specialized labs using rather complex test equipment, often including real-time simulators. Such testing is mostly focused on requirements in accordance with the existing standards, which are mostly focused on components/subsystems.
Provided that the equipment has been type-tested to assure that the functionality fulfils the requirements of the applicable standards, for both its accuracy and interoperability with other equipment, currently performed commissioning tests are likely to be minimal, consisting of checks on magnitude and directionality, the local settings of the device (sampling rates for example), and the correctness of the time stamping.
The end-to-end testing is not commonly used at the acceptance level due to its complexity and requirements for in-field testing tools and procedures. Since the existing synchrophasor installations still experience substantial bad data issues (NASPI Report 2017-TR-002, “PMU Data Quality: A Framework for the Attributes of PMU Data Quality and a Methodology for Examining Data Quality. Impacts to Synchrophasor Applications”), it is prudent to explore how such issues may be detected at the commissioning and in-service stages of life-cycle management.
Special attention should be paid to the issue of backward compatibility and interoperability and how such requirements are validated using lab and/or field testing.
The brochure then discusses life cycle testing requirements practiced in several countries: Brazil, China, India, Finland and Russia. The requirements for the systems that lead to the testing practices are elaborated in the brochure appendices, which highlight the requirements from the mentioned countries. Based on the practices, it is evident that commissioning and in-service tests are needed. While the commissioning tests are performed, it is not clear how individual upgrades to the system are commissioned, i.e., it is not clear whether the entire system would need to be re-commissioned after major upgrades. Also, it was noted that the interoperability testing was not pursued since the vendor compliance to individual standards was deemed sufficient to guarantee the level of interoperability among different synchrophasor system components.
It appears that the commercial testing tools are sufficient to perform the commissioning and in-service test. Examples of worldwide suppliers of PMU test equipment are Omicron, Doble, and Fluke. Doble precise signal generator and Fluke PMU Calibrator 6135A are used in field and lab testing, respectively. Omicron’s CMC 256plus protection relay test set is recommended by Omicron for both field and lab testing. Since the end-to-end testing was not explicitly mentioned as the requirement, no tools that may be used for such testing were defined.
The brochure ends with several recommendations:
- Regarding standards, the IEEE standard most relevant to this recommendation is the revised version of the standard "IEEE Guide for Synchronization, Calibration, Testing, and Installation of Phasor Measurement Units (PMUs) for Power System Protection and Control", IEEE C37.242-2013 to be published in 2021. If a country has more detailed standards that guide such testing steps, these standards should supplement the IEEE standards. Detailed IEEE and/or IEC testing standards and methods are needed in the future.
- As the PMU gets applied to more critical real-time applications such as control and protection, more rigorous testing practices should be developed, particularly for in-service testing. As of now, the lack of testing tools and procedures for in-service tests is apparent. The end-to-end testing that includes applications is not well defined either. It is highly recommended that end users explore the need for end-to-end testing, keeping in mind that real-time applications have rather tight performance requirements that need to be assured at all times for successful operation that uses such applications.
- It has been recognized that end-users do not have enough highly qualified staff that may be deployed to calibrate, test, maintain and monitor the performance of the synchrophasor systems. It is recommended that such practice be changed by recognizing the importance of testing and allocating adequate resources to perform related tasks. This practice and its importance for successful deployment of synchrophasor system should be revisited frequently to determine whether any procedures and relate test equipment need to be updated, and consequently, whether their staff need to be trained/re-trained. The role of academic institutions in the training programs is highly encouraged.
- It is highly desirable that future Study Committee B5 efforts in the synchrophasor life-cycle management area are focused on the distribution PMUs (DPMUs). This area is rapidly expanding and yet has different requirements than the transmission applications. In many countries around the world, DPMUs projects are underway, and the industry needs guidance regarding lifecycle management, so forming a WG to address such issues will be timely.
The brochure ends with a suggestion for future steps:
- a) End users should persist in looking at the synchrophasor systems in a holistic way by defining the life-cycle test and calibration procedures;
- b) Vendors should be ready to offer and perform interoperability tests as needed to verify that end-to-end legacy systems may be upgraded with a variety of products on the market going forward;
- c) Standards organizations should develop procedures for application testing that will also encompass end-to-end testing of the underlying synchrophasor infrastructure; and
- d) Consultants, vendors, and academic researchers should look into the fundamentals needed to better understand the synchrophasor system performance under transient conditions and recommend adequate calibration and test procedures beyond what is currently defined in the standards.