Recommendations for testing DC lapped cable systems for power transmission at a rated voltage up to and including 800 kV
HVDC cables with lapped insulation have been in operation for nearly 70 years since the first 100 kV HVDC cable went into service in 1954. CIGRE has developed test recommendations for lapped HVDC cables in parallel with the development of the technology to higher voltage levels. The latest updated test recommendation was published in ELECTRA No. 189 “Recommendations for tests of power transmission DC cables for a rated voltage up to 800 kV” in 2000. The recommendation was supplemented by an addendum published in ELECTRA No. 218 in 2005.
Convenor
(NO)
G. EVENSET
Secretary
(NO)
N. KRISTJANSDOTTIR
H. WANG (CN), L. LERVIK (NO), O. HANSSON (SE), D. DUBOIS (FR), B. PAILLER (FR), G. MIRAMONTI (IT), A. TROLLI (IT), G. LAGROTTERIA (IT), V. FOO (JP), K. BUN TSE (DE), K. SEONG-WEON (KR), R. SVOMA (UK)
Corresponding Members: G. TZEMIS (UK), C. ZHENGZHENG (CN)
Introduction
The HVDC technology has developed significantly since said recommendations were published and Cigre study committee B1 decided to launch working group B1-66 “Recommendations for testing DC Lapped Cable Systems for power transmission at rated voltages up to and including 800kV” to merge the existing recommendations published in Electra papers into a technical brochure and update the test requirements considering the recent development of HVDC technology.
The work has been performed in parallel with other working groups also working on issues related to testing of HVDC cable systems. In particular, JWG B4/B1/C4.73 “Surge and extended overvoltage testing of HVDC Cable Systems” which has analysed the transient overvoltages occurring in HVDC systems with voltage source converters. The work in this working group has provided valuable input to updating transient voltage testing of HVDC cable systems. In addition, the work has been aligned where relevant with the work performed in WG B1.62 “Recommendations for testing DC extruded cable systems for power transmission at a rated voltage up to and including 800 kV”.
The Recommendations are applicable to paper insulated cables, i.e., mass-impregnated cables with kraft paper or polypropylene laminated paper and oil-filled pressurised cables. They can be used also for other cables with lapped insulation.
Description of the Technical Brochure
The Technical Brochure includes recommendations for development tests, prequalification tests, type tests, routine tests, sample tests, special temporary overvoltage tests and after installation tests.
Chapter 1 provides an introduction to the subject, the scope and limitations of the recommendation and definitions.
The updated recommendation applies to cables and accessories, either submarine cables or land cables, intended to be used in DC power transmission systems with rated voltages up to and including 800 kV between conductor and ground. The Recommendations are applicable to paper insulated cables, i.e., mass-impregnated cables with kraft paper or polypropylene laminated paper and oil-filled pressurised cables. They can be used also for other cables with lapped insulation.
These Recommendations do not cover HVDC cables with extruded insulation.
The first chapter also defines requirements to the type test objects and the test loops, see Figure 1. Controlling end effects are very important during type testing/prequalification testing of non-pressurized mass-impregnated cables and the requirements from ELECTRA No. 189 “Recommendations for tests of power transmission DC cables for a rated voltage up to 800 kV” has been maintained. The manufacturer should demonstrate that the test method does not cause axial flow of impregnation compound that may impact the dielectric properties of the objects under test.
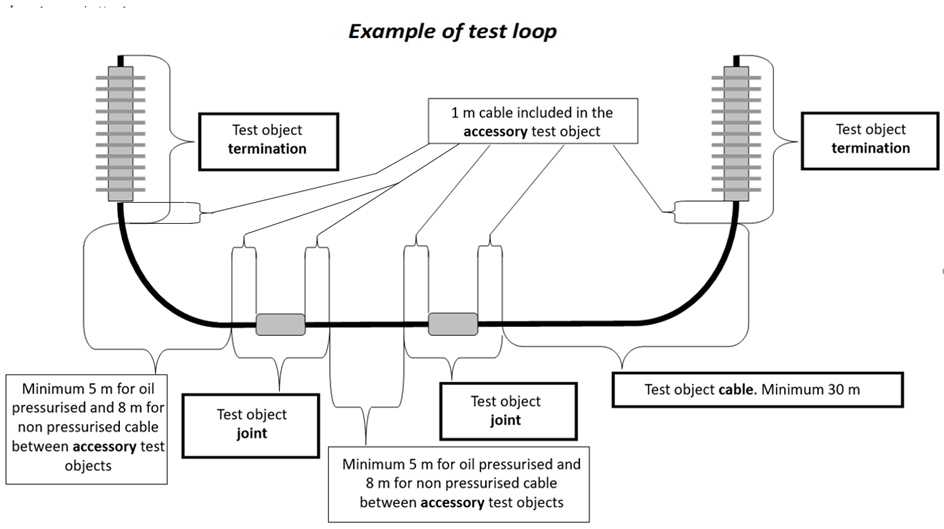
Figure 1 - Example of a test loop including extension of test objects
A new and better definition of voltages is included in the new Technical Brochure.
Chapter 2 provides a list of possible development tests that may be performed prior to commencing prequalification tests or type tests. The extent of the development work and tests are left at the discretion of the manufacturer.
Chapter 3 provides recommendations for prequalification tests to be performed for new insulating materials. This is a new test for cables with lapped insulation and is not intended for kraft paper insulated mass-impregnated/pressurised cables from manufacturers with previous service experience.
New lapped insulation materials may be introduced in the future and the working group concluded that a prequalification test would be required to prove the long-term properties of new insulation materials.
The requirements for the prequalification test are similar to the requirements for extruded cable systems and the duration of test is 360 days.
Recommended test sequences are provided for cable systems to be qualified for operation with line commutated converters involving polarity reversals and for cable systems to be qualified for operation with voltage source converters. A cable system prequalified for operation with line commutated converters (LCC) is also prequalified for operation with voltage source converters (VSC).
Chapter 4 provides recommendations for extension of qualification of kraft paper insulated mass-impregnated cables. This is a new test for mass-impregnated cables intended to verify major changes in operating operating conditions compared to previous service experience. Such changes may be significant increase of operating temperature, electrical stress, voltage level, etc.
The recommended test sequence has been peformed in several projects to verify major changes in operating conditions for line commutated converter systems. A similar test sequence is also recommended for cable systems with voltage source converters. A cable system qualified for operation with line commutated converters is also qualified for operation with voltage source converters.
Chapter 5 provides recommendations for type tests. The new recommendationw include test requirements for cable systems in VSC systems where the cables are not exposed to polarity reversals. The tests introduced for voltage source converters follows the same principle as in the test recommendations for extruded DC cables and the test duration is identical to LCC systems.
The switching impulse test recommendation has also been updated to reflect the requirements for cables operaing in VSC systems.
Two new non-electrical type tests have been introduced in the updated recommendation.
Firstly, a longitudinal water penetration test for non-pressurised cables is recommended to be performed to assess the longitudinal water propagation properties of the cables. The information from this test can be used to estimate the length of cable that has to be cut to ensure moiture free cable before commencing a jointing operation.
Secondly, measurement of specific thermal resistivity of insulation system is recommended to verity the design value used in rating calculations. The specific thermal resistivity at maximum operating temperature for modern mass-impregnated cables is not standardized and the actual value should be proved by testing.
Chapter 6 provides recommendations for routine tests. The routine tests and sample tests have been separted into chapter 6 and 7 in the updated test recommendation.
The duration of the HVDC tests has been increased from 15 to 30 minutes based on experience from recent projects.
Chapter 7 provides recommendations for sample tests. All sample tests from the previous recommendations are included in this chapter and some new tests have been added.
Chapter 8 provides recommendations for testing the cable systems for the transient overvoltages which are not covered by the standardized lightning impulse and switching impulse. These are new tests and it is not the intention that all tests described in this chapter are automatically part of the testing regime for HVDC cable systems, but more an exception to study and/or address project specific issues or for engineering information. According to the work of CIGRE JWG B4/B1/C4.73, two new overvoltages can be experienced on HVDC cable systems on top of conventional lightning and switching impulses. The two identified voltages are very slow front overvoltages with same polarity as the DC voltage and oscillating overvoltages with opposite polarity peaks to the actual DC voltage. These overvoltages may occur when there are earth faults in the systems and as such are not expected to occur many times during the systems lifetime. The actual magnitude and duration of the overvoltages depends on the HVDC system configuration and the protection included in the systems.
The recommended wave shapes are as far as practicable designed to reproduce the envelope of the overvoltages identified by CIGRE JWG B4/B1/C4.73 recognizing that there are limitations in laboratory equipment that can produce the wave shapes.
The proposed wave shape for the very slow front overvoltage with same polarity to actual DC voltage is shown in Figure 2. This voltage may occur on the heathy pole when a ground fault occurs on the other pole. The time to peak, T1, is recommended to be in the range 1-3 ms and the time at voltage above 90% of the peak voltage, T2, is recommended to be in the range 10-150 ms.
Figure 3 shows the recommended wave shape for testing the cable system for oscillating damped temporary overvoltage. This voltage may occur on the faulty pole during a ground fault. The time between two damped oscillations, T4, and the number of zero crossing damped temporary overvoltage oscillations before the peak voltage falls below 5% of U0, n4, is recommended to be agreed between the manufacturer and the customer.
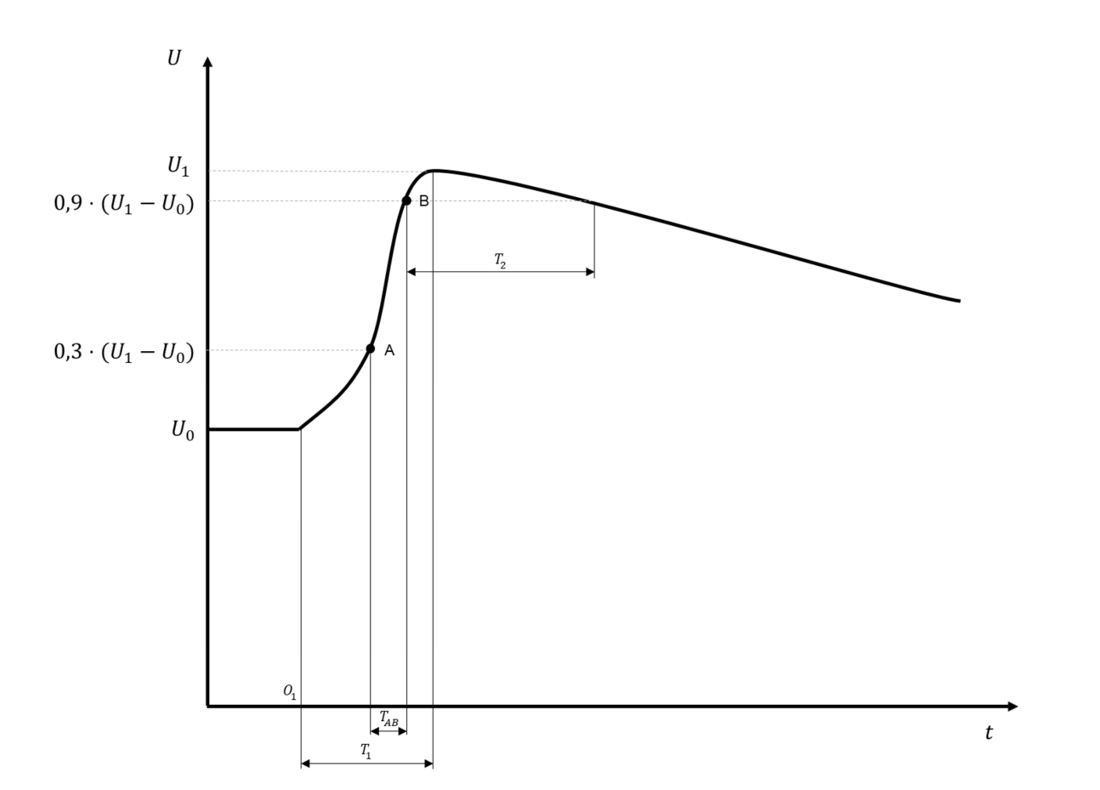
Figure 2 - Very slow front temporary overvoltage
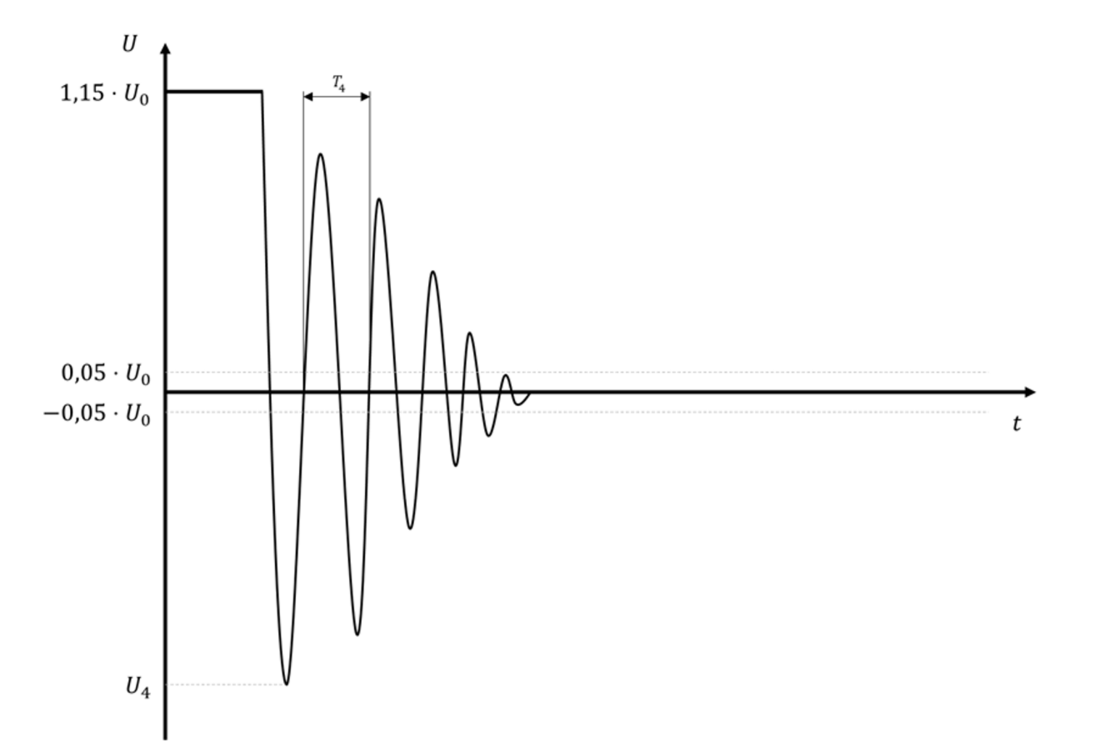
Figure 3 - Zero crossing damped temporary overvoltage
The special temporary overvoltage test is aligned between this recommendation and the recommendation for extruded HVDC cables prepared by Cigré WG B1-62. However, there are some differences. The requirements for preconditioning before the tests are aligned with the requirements in the type test regarding resting time between load cycles are different polarity.
The zero-crossing damped overvoltage test on lapped insulation systems shall be performed when the cable system is cooling from its maximum temperature. The reason for this criterion is the cable system should be subjected to the oscillating voltage when the pressure in the cables is decreasing and when cavities are formed of growing in the impregnation compound of non-pressurised cables. The oscillating voltage may cause partial discharges in cavities and ageing of the insulation system.
Chapter 9 provides recommendations for after installation tests. The duration of the HV test has been increased from 15 minutes to 30 minutes.
Conclusion
The test recommendations for testing DC lapped cables published in Electra No. 189 and 218 have been combined in one new technical brochure and test recommendations have been updated to reflect the current requirements for cables operating in LCC and VSC HVDC systems. Guidelines for qualification of new insulation materials and extension of qualification in case of major changes in operating conditions of existing insulation systems have been included. These updates will provide good support for testing DC lapped cable systems for coming projects and qualification of cable systems up to 800 kV service voltage.