Impact of Covid-19 to System Operators and Electrical Equipment Manufacturers
The COVID-19 pandemic which began late 2019, beginning of 2020 brought a new aspect affecting world´s economy. Players of different industries were not used to global catastrophes, but rather geographically circumscribed ones. The measures taken all over the world to slow down the dissemination of the virus, mostly concentrated on social distancing. In some extreme cases quarantine was applied to the population in regions with high contamination indexes. Both national and local health authorities were deeply involved in monitoring the contamination curves as well as applying and continuously adapting control rules for social contact and working environment.
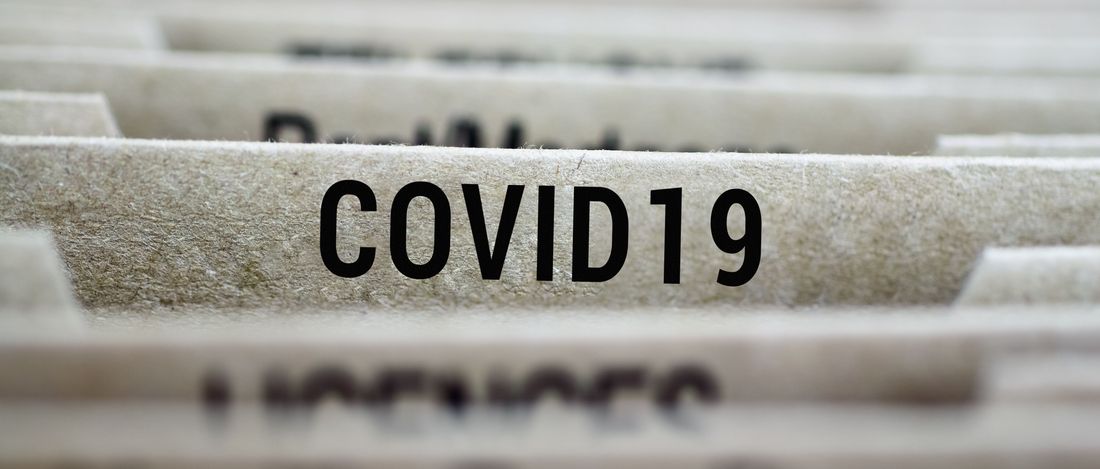
CIGRE Utility Advisory Group A3
By Nenad Uzelac (US), Frank Richter (DE), Antonio Carvalho (BR), Robert le Roux (IE), Pavel Novak (DE), Jorge Amon (BR)
In the power industry, the direct effects of COVID-19 resulted in a reduction of field services in general, specifically maintenance services. In many cases services have been postponed or extended in time to completion. The direct effect of this could be an increased risk of equipment failure. On the other hand, the verified reduction of system load, between 10% and 30% of the load before pandemic, helps to keep service continuity under control. Figure 1 gives a clear picture of system load behavior in 2020 compared to the same time span of 2019. As a consequence of load reduction, energy prices in general dropped causing, unexpected financial problems for Generation Companies, Energy Traders, TSO´s and Distribution utilities.
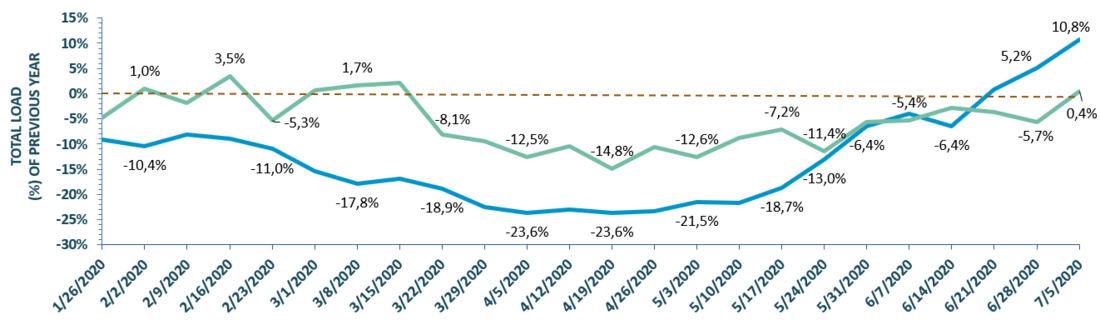
Figure 1 - Daily load drops in USA (blue) and Brasil (green)
[Source: https://www.eia.gov/realtime_grid/?src=data#/summary/demand?end=20200423&start=20200416]
Having this unusual scenario in mind CIGRE Study Committee A3 – Transmission & Distribution Equipment collected information worldwide from transmission and distribution utilities, as well as HV equipment manufacturers to investigate the effects of the COVID-19 pandemic on their daily business and measures taken to overcome the problems faced. In parallel a questionnaire was conveyed in the industry. The full results of the survey are available at CIGRE SC A3 website.
The compilation of the collected information together with a consolidation of the impact on the global electricity sector and the measures taken by Utilities and system operators during the pandemic are presented in this paper. Full article with comprehensive information is published in CIGRE Science & Engineering journal (October 2020 edition).
Impact of the restrictions applied to system operators and the supply chain
In all global industries, personnel and personal safety is the highest priority, which gets even more underlined under working conditions during pandemic times. Many companies and institutions whose activities are mainly organized as teamwork in offices or meeting rooms have allowed their employees to work from home, a practice known as home office. While in typical companies the internal processes and functions can be ensured remotely or outsourced, Utilities face a unique challenge in comparison to the others. The workforce being critical for the continued operation of the business, and the safe and reliable delivery of electric power becomes a spotlight.
Several security actions have been taken to preserve the corporate environment of the Covid-19 pandemic by big utilities in Brazil and Ireland. The companies have adopted numerous contingency measures that have been shown to be effective in its offices and in the areas of operation of plant and substations. The measures were ranging from provision of protective materials, activation of redundancy structures in Operation Centers and the Telecommunications Supervision Centers, over to organization of employee working regime. The most restricted arrangements were put in place for Network Technicians and Dispatchers. They were only allowed to go directly to site from home, and returning home after any site visit. Food and drink were provided to them in accordance with special safety procedure. Further, control rooms are being disinfected after every shift, and even special policies of shifts including reduced number of dispatchers during shift or keeping reserve shifts in isolation are organized.
Supply chain problems are influencing the schedule of ongoing projects or short-term intervention plans, as identified by the survey carried out. Though supply issues have already emerged to a certain extent, the industry as a whole has overcome these. Most utilities and system operators stated that, delays in supply chain have not been a significant issue so far. This is the result of identifying manufacturers as providing essential services, so the equipment production delays are under control. The major concern remains mid-to long-term uncertainties, due to border closure and travel bans during any future regional pandemic lockdowns.
In global context, maintenance of electrical equipment at generation, transmission and distribution level during pandemic is limited. Priority is given to the maintenance of critical elements, unplanned outages and ensuring electricity supply to healthcare facilities (e.g. hospitals) and temporary quarantine centres.
Impact to product qualification and factory tests
Development of new products comes along with a variety of tests. Type tests are performed before the product is launched on the market and in accordance with international standards to ensure reliable equipment application in power transmission and distribution. There is a limited number of test laboratories that are capable to perform all tests as required by the standards and for the execution test, objects need to be shipped to the laboratory. Development engineers and testing experts from the manufacturer typically travel to the laboratories to prepare test setup, execute and supervise the test process or attend the visual inspection after test execution together with experts from the laboratories.
COVID-19 has made product qualification quite challenging due to travel restrictions, local regulations or social distancing rules. In order to continue with development and testing activities, while ensuring personal safety some labs have established remote testing programs. In a nutshell, “remote testing” means shipping the test-object to the testing laboratory while the experts from the manufacturer stay at home and are given the opportunity, through IT systems, to witness, support and evaluate the tests remotely.
As an example, testing of a medium-voltage breaker was performed in KEMA Laboratory in Netherlands, with manufacturer experts connected from USA. The breaker to be tested was assembled by the manufacturer and shipped to the lab. During test execution phase a close collaboration between manufacturer and lab is essential: to review and agree on the test plan, inspect the test circuit and test parameters. Communication between the lab engineer and expert from manufacturer can be done by conferencing tools which are well known from online conferencing. Additionally, videos, including slow-motion, from the remote-controlled observation cameras are shared online. Once the testing starts, the remote engineers need to have immediate access to the measured data. Remote desktop applications or sharing data on a common drive are two ways to realize this. With remote desktop applications the client controls the remote computer from his local computer. Upon completion of the type test, visual inspection was performed, using ‘Hololens’. In this way manufacturer could follow and comment to test engineer directly on the product. The remote testing campaign is illustrated in figure 2.
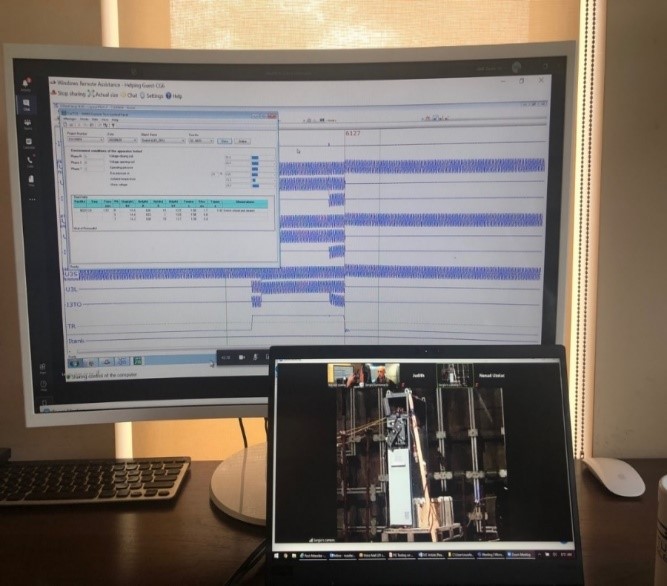
Figure 2 - Remote desktop with real time data and video stream of test
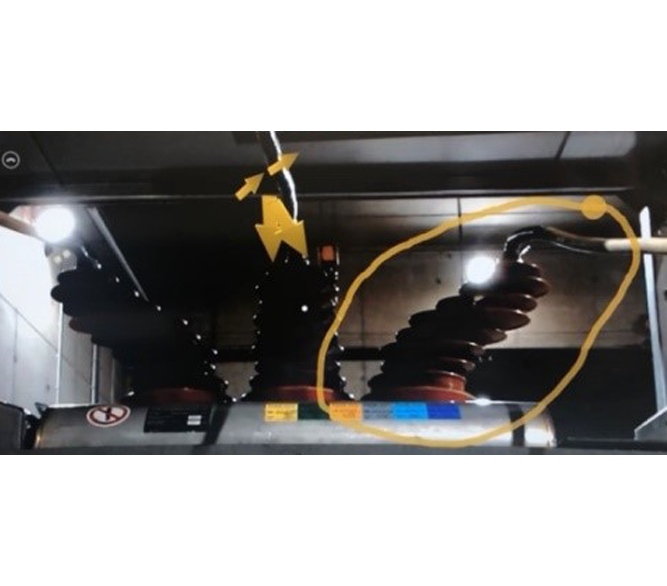
Figure 2 - Manufacturer guiding of test engineer through Hololens
Another point is linked with product inspection and final quality assurance through users. Such activity generally requires the end user to be on-site due to down time needed for test setup and movement of equipment. Due to manufacturers´ site access restriction, also here remote solutions for factory acceptance tests were implemented.
G&W Electric Company leveraged corresponding technology and teamwork to meet customer demand for witnessed testing, while still practicing social distancing guidelines. In the initial stages of the outbreak, G&W Electric Company’s Order Management group teamed up with its Marketing department to produce a short film that documented each of the routine tests associated with the customer’s SF6 switchgear. This included the high voltage one minute withstand test, circuit resistance test, visual inspection, and the full script of relay test steps needed to prove the automation associated with the switch. Social distancing was easily practiced as only 3 people were required to complete the entire production. The completed film consolidated all activities and allowed the customer to witness each of the required tests in approximately 1 hour with no travel requirement.
Further, virtual meeting technology such as Zoom and Go-to-meeting to provide a more interactive experience for customer witnessed testing was deployed. Large groups from multiple locations were able to enter virtual meeting rooms while G&W team members broadcast real time activities from their computer screen. HD video camera mounted on a tripod was used to capture the overall equipment setup, while handheld smart phones or tablets were used to provide live close-up feeds of the equipment.
In general, same procedures were established throughout the industry. Insight to remote factory acceptance test (FAT) is given in figure 3.
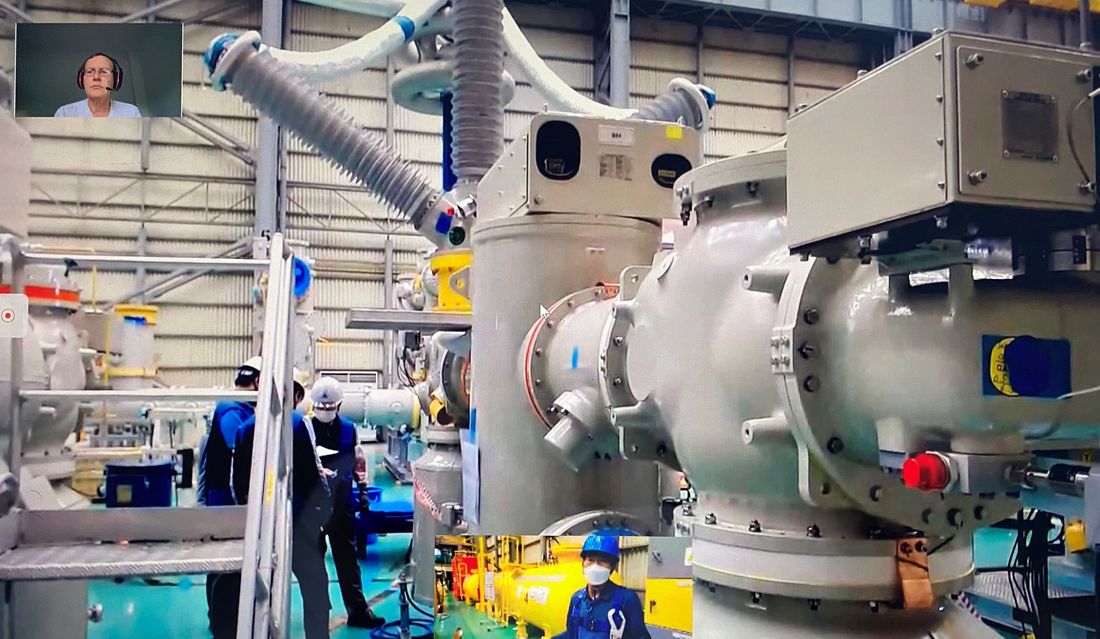
Figure 3 - Ongoing routine tests on manufacturer side of HV switchgear. Camera view from tester´s hard hat
Financial impact on system operators & manufacturers
Slowdown in economies strongly impacts the industry. An example on Brazilian economy shows the financial impact, which are illustrative in global scale. Fall of electricity consumption, is considered from an "optimistic" scenario with 4.7%, over to a "pessimistic" scenario with a 12.3% drop. The projections take into account a 3.6% decline in Brazilian GDP (Gross Domestic Product) in the optimistic scenario and a 9.5% decline in the economy in the pessimistic view. Energy traders expect a negative impact of R$ 5 billion this year due to these requests for flexibility and the lower consumption by their customers as a result of the pandemics [1].
Most of Europe adopted some form of lock-down and several countries have already started relaxing rules since June 2020. For 2021 the GDP forecast shows positive growth, but lower than the 2020 drawback, as shown in Figure 4.
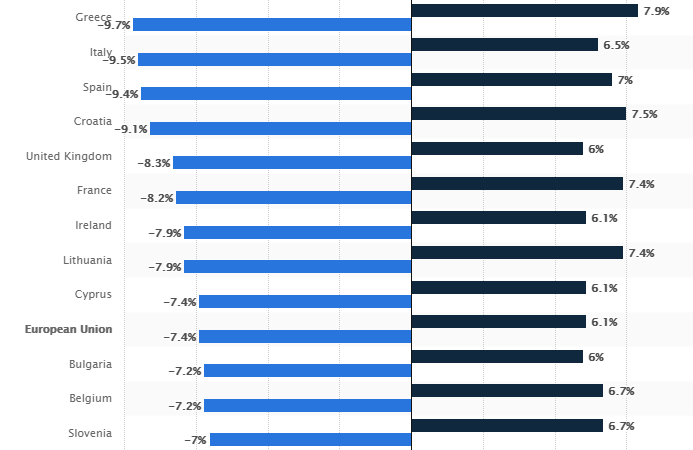
Figure 4 - GDP forecast for some European countries for 2020 and 2021, by statistic
[Source: https://www.statista.com/statistics/1102546/coronavirus-european-gdp-growth/#statisticContainer]
Conclusion
In summary, system operators, energy companies and equipment manufacturers mobilized their capabilities and resources to maintain critical infrastructure and business continuity during the COVID-19 pandemic. Priority remained the health and safety of the employees, users and partners. Manufacturers utilized remote testing for qualification of electrical equipment and FAT. The added valued of Digitalization, remote assistant and online video tools could be demonstrated. In this way, the limitations enforced by the COVID-19 situation can increase efficiency and reduce costs.
No COVID-19 network congestion issues or problem with security of supply have been reported in Europe´s systems. The pandemic has given direct evidence of appropriate protection methods used by system operators. It can be envisaged that all system operators will come out strengthened. The true impact of Covid-19 is still to be determined, however some plans for post-COVID-19 recovery that promote sustainable growth through the green and digital transition are already created [2].
Acknowledgements
The authors would like to express their gratitude to Rene Smeets (NL), Martin Kriegel (CH), Marta Lacorte (BR) and Andre Mercier (CA) for their valuable contribution to this paper.
- [1] Consumo de eletricidade no Brasil pode cair até 12% em 2020, diz consultoria, g1.globo.com, May 25th 2020. Available at g1.globo.com/economia/noticia/2020/05/25/consumo-de-eletricidade-no-brasil-pode-cair-ate-12percent-em-2020-diz-consultoria.ghtml
- [2] System Operations impact of Covid-19: European Perspective, CIGRE, June 02nd 2020. Available at www.cigre.org/article/GB/system-operations-impact-of-covid-19-european-perspective