Transmission lines with Fiber Reinforced Polymer (FRP) composites
For a long time traditional material such as wood, steel, and concrete were used for transmission line structures. Advancement in material science and demand for solutions in the aerospace and maritime industries led to the development of new high-tech materials with properties that could also be beneficial for the electrical utility industry. One such class of emerging materials are Fiber Reinforced Polymer Composites (FRP). Different manufacturing methods and shapes make it possible for designing a great variety of structural elements.
Convenor
(IS)
A.B. JONASSON
Secretary
(CA)
J. TOTH
C.G. BARRIOS (ES), J. BARTSCH (SE), T. BJARNASON (IS), D. CHAMBERS (UK), J.B. DA SILVA (BR), V. DALE (NO), P. DE HORA (IE), P.W. DULHUNTY (AU), M. ERMOSHINA (RU), G FECHT (CA), M. HUGHES (US), S. LABOCHA (PL), S. LANGLOIS (CA), F. LIRIOS (AU), J. LUCEY (IE), L. NAZIMEK (PL), E. PLATENKAMP (NL), X. POLETTA (FR), A. RUFFIER (BR), B. WAREING (UK), O. WELGAARD (NO),
Corresponding Members: A. BANGOR (AU), F.K. GBEDEY (BJ), R. GEARY (IE), T. GILLESPIE (AU), C. HUGHES (IE), D. LOUDON (NO), A. MOGILEVSKY (CA), M. RAMASWAMY (IN), V. ROULET (FR), D. SMAZNOV (RU), O. SEMENKO (UA), K. VALIMAA (FI)
Reviewers: M. ELLENBOGEN (IL), W. TROPPAUER (AT), K. VALIMAA (FI)
What are glass Fiber Reinforced Polymer composites?
Fiber Reinforced Polymer composite materials have two major components. Fibers and the resin system the holds the fiber system in place. Other components may be added to the system such as fillers, Ultraviolet (UV) inhibitors, and property-enhancing additives.
Resin systems
Resins are solid or highly viscous substances that are converted into polymers. When converted to polymers they solidly hold together the other components, such as the fillers, modifiers, additives and the fibers. For transmission lines typically two major resin systems are used, Vinylester and Polyurethane. Each has some advantages and disadvantages, but overall properties serve the transmission line structures very well.
Fibers
Many different types of fibers could be used for polymer composites, such as carbon, glass, basalt, and aramid. Due to cost, availability, chemical, electrical and mechanical properties E-Glass fibre is the primary reinforcement for the composite materials used for transmission lines. E-glass is electrically non-conductive, inexpensive (about 1/10 of the cost of carbon fiber) and has good mechanical properties for transmission lines.
Manufacturing methods of fiber reinforced polymer composite transmission line structures structures
There are three major manufacturing methods used for making FRP transmission line components; Filament Winding, Pultrusion and Centrifugal Casting.
Filament winding
Filament winding is the open mould manufacturing practice of wrapping resin saturated fibers around a tapered or cylindrical mandrel. A typical laminate wind schedule consists of opposing circumferential wraps in which the manufacturer will usually have the ability to adjust the fiber placement angle (Figure 1).
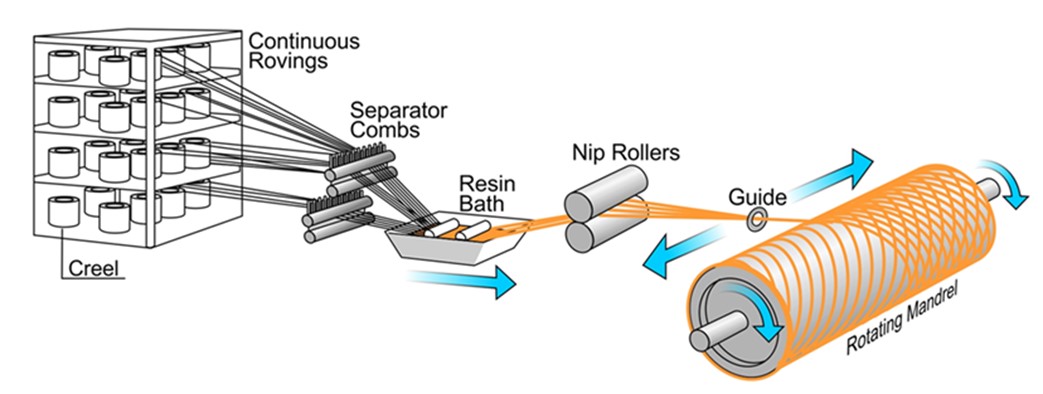
Figure 1 - Illustration of Filament Winding Process
The pultrusion process makes constant cross section, cut-to-length pieces that can be used for a variety of structural components (Figure 2):
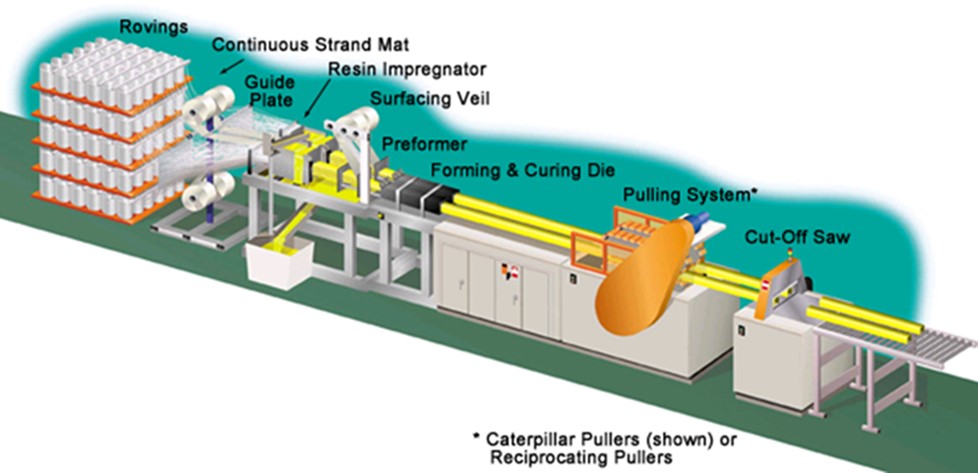
Figure 2 - Illustration of Pultrusion Process
The cross sections could be either round, rectangular or polygonal. A great variety of shapes could be made with pultrusion for transmission lines (Figure 3):
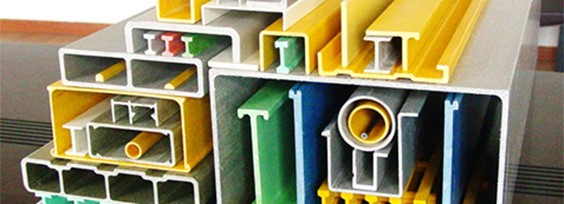
Figure 3 - Pultruded FRP Cross Sections
Centrifugal casting
Spun fiberglass poles with round cross-section are made of glass-fiber complexes and polyester resin and are produced with a centrifugal process (Figure 4).
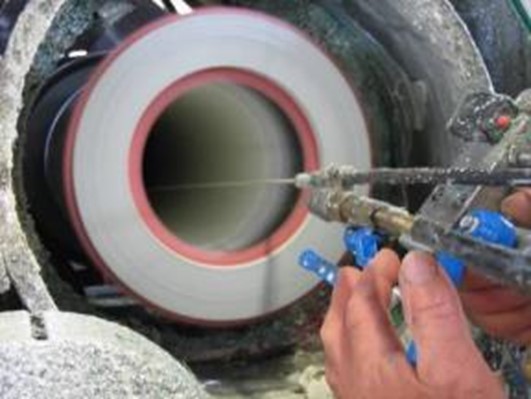
Figure 4 - Image of Centrifugal casting of FRP pole
The use of FRP for transmission line structures
There are many advantages of using FRP structures for transmission lines, such as long service life, resistance to corrosion, light weight, high specific strength, high dielectric strength, dimensional stability, fire resistance, environmental inertness, resistance to animal damage (such as woodpeckers), engineered product, ductile, and lower overall life cycle cost compare to other materials. Further details are available in the Technical Brochure 818.
High dielectric strength
FRP materials have such a high dielectric strength that they are considered electrically insulating. This makes them very desirable for increasing safety for live (energized) work. Moreover, the electrical characteristics and lightening performance of the lines with FRP structures are better than the line made of traditional materials.
Light weight
FRP transmission line structures are much lighter than wood, steel or concrete elements made for the same function. Transportation and installation costs are reduced as lighter equipment is sufficient for construction and larger quantities of material can be shipped with the same transportation method then with the other materials (Figure 5). In addition, it is often possible to manoeuvre FRP utility poles by hand into restricted locations (Figure 6).
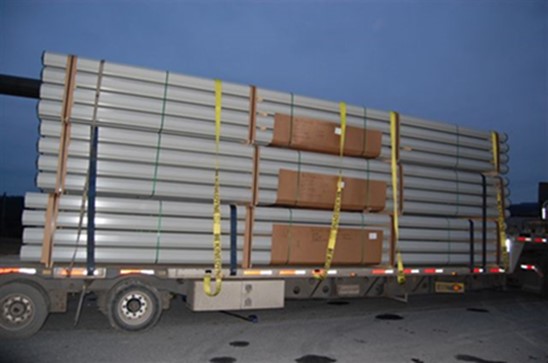
Figure 5 - Large number of FRP poles shipped with one truck to site
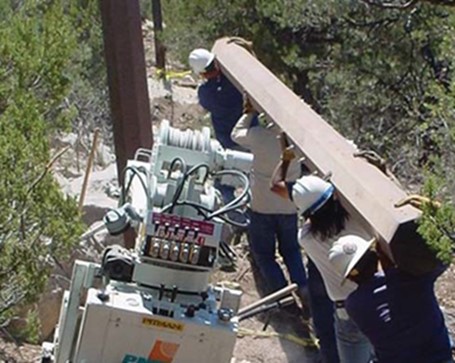
Figure 6 - Shoulder carrying of FRP pole to installation site
No rot, spall or corrosion
FRP materials can withstand environmental conditions much better than the other materials, even in harsh climates and polluted areas
Environmentally inert
FRP materials are environmentally inert, do not leach out components to the surroundings. Even if disposal is needed, they could be placed in regular landfills due to their chemically neutral properties.
Unaffected by termites, woodpeckers and vermin
FRP materials can resist insects, woodpeckers and other animals well. In many areas where woodpeckers damage wood poles FRP poles are the replacement of choice.
Long life span
When the Ultra Violet protection is properly addressed FRP structures last much longer without any intervention compared to traditional materials.
Stiffness
FRP materials have lower modulus of elasticity than steel or wood [1], as a result of which their stiffness value is different, and they deflect differently. The stiffness value, which determines deflection is influenced by two components, the modulus of elasticity and cross section properties. When designing FRP elements, the design needs to consider both and compensate as needed.
FRP transmission line structures
There are many structural elements that can be built using FRP materials that are similar to structures made of wood, steel or concrete. The most common structures are poles, cross arms, cross bracings, foundations, anchors, piles and lattice towers.
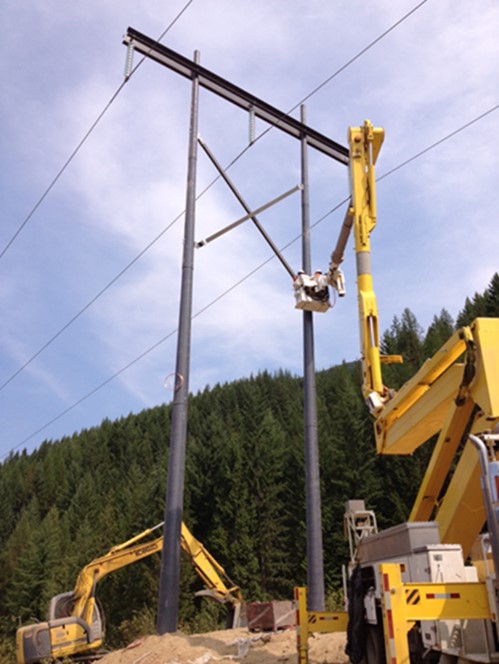
Figure 7 - 230 kV FRP Composite H-frame with FRP poles, cross arms and cross bracings
Poles
The most widely used FRP transmission line structures are poles. Several suppliers make filament winded, pultruded and centrifugal casted poles. Usually the cross section is round, but there are also poles with octagonal shape.
Cross arms
There are FRP cross arms made of boxed and channel cross sections. Their usual application is to replace exiting wood cross arms.
Cross braces
Cross braces made of FRP could be used with H-frames. An example of an FRP cross bracing on a fully composite H-frame is shown on Figure 7.
Anchor logs
Traditional anchor logs (in some countries called sleepers) are made of wood. FRP log anchors can replace wooden logs providing a cost effective, light weight and durable alternative to the original design.
Piles and Sheet piles
Since piles and sheet piles are constant cross-sectional elements, they can be made using FRP Pultrusion manufacturing.
Lattice structures
Three 230 kV FRP lattice structures have been in service in California, USA in a highly corrosive seashore environment since the mid 1990’s (Figure 8). Their easy and fast assembly, and great resilience in the corrosive environment provided great value for the utility that installed them.
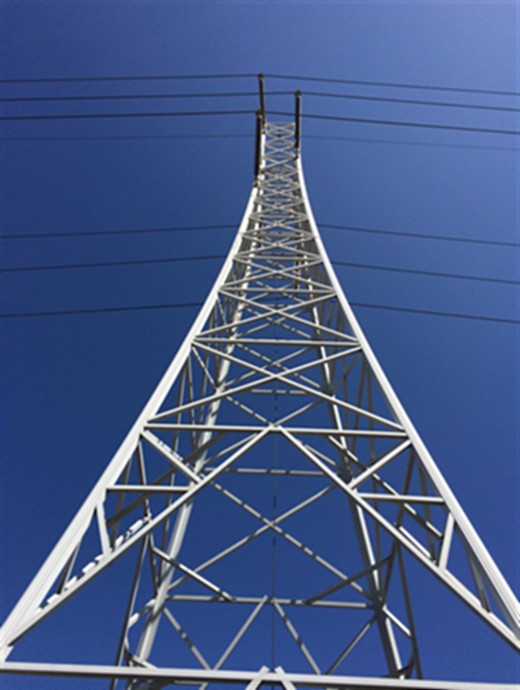
Figure 8 - 230 kV FRP lattice structure
FRP transmission line structures cost comparison
The CIGRE Brochure 818 has a very detailed section comparing the cost of FRP structures to wood and steel structures. The overall conclusion is that FRP structures are good and cost-effective alternatives to wood, steel and concrete structures.
Conclusions
Fiber Reinforced Polymer composite structures for transmission lines are new to the electrical utility industry. However, the aerospace, maritime, bridge and light commercial industries have been using FRP for a long time with great success.
FRP provides a cost effective, environmentally friendly, durable and reliable solution for many of the challenges the electrical utility industry faces.
Educating the transmission line community on the benefits and use of FRP is essential to make the use of this technology wide spread.
The CIGRE Technical Brochure 818 is a great tool in this effort, and is a highly recommended reference for professionals in this field.