Rotating electrical machines
by Kevin Mayor, Chair & Peter Wiehe, Secretary
Introduction
Study Committee A1 covers all aspects of rotating electrical machines associated with power generation ranging from research, development, design, manufacture and testing of new machines to commissioning, operation, condition assessment, maintenance, refurbishment, upgrades, conversion, storage and de-commissioning.
SC A1 considers 4 technology groups based on the application of rotating electrical machines; Turbo-Generators, Hydro-Generators, Large and High Efficiency Motors and New Technologies. Each of these groups is concerned with the international exchange of information, knowledge, practice and experience on rotating electrical machines.
The Study Committee has 24 Regular Members, 6 Additional Regular Members and 14 Observer Members representing 37 countries across all continents. They are complemented by over 300 experts from utilities, manufacturers, consultants, research centres and universities who all contribute to SC A1 activities including Working Group, committee meetings, symposiums, colloquiums, tutorials and webinars.
Key focus areas within Study Committee A1 are embodied in the strategic directions which are regularly reviewed to ensure relevance to the changing power generation landscape.
Strategic Directions of SC A1
The activities of the Study Committee have been driven by the following six key main Strategic Directions:
- SD 1: Asset Management
- SD 2: Machine/System Interaction
- SD 3: Renewable Generation
- SD 4: Motors
- SD 5: Machine Monitoring, Diagnosis and Prognosis
- SD 6: Efficiency of Electrical Machines
Specific activities addressing these strategic directions and forward-looking opportunities are explained below. The full list of current Working Groups and publications are given in Tables 1 and 4 at the end of the report.
SD 1: Asset Management
Asset management covers a broad range of aspects relating to the ownership, operation, condition assessment, maintenance and repair, upgrade, conversion, replacement and storage of rotating electrical machines including strategic spares.
Asset management of power plants requires critical decisions to be made balancing the different options available to maintain and improve asset and power system performance and reliability. Commercial and technical decisions range from the repair of components, major refurbishment, total replacement or duty conversion of a generator or motor. Extending the service of a turbo-generator beyond the typical design life of about 30 years (over 50 years for hydro-generators), requires a knowledge of the service history of the generator type, the success of repairs of known issues, and an ability to confidently predict the remaining service potential, associated costs of monitoring and maintenance and operational limitations. When considering replacement, the capital outlay must be weighed against the operational benefits and income that may come from increased output, efficiency, and improved capability and availability for grid support. In some cases older plant, whose MW output is no longer needed due to the implementation of renewable generation sources, have been converted to synchronous compensator duty as a cost effective alternative to installing new, non-rotating VAr compensation or energy storage equipment with the added benefits of mechanical inertia and short circuit power improving fault ride-through capability. This aspect is further discussed under SD 3.
There are currently 10 active Working Groups dealing directly or indirectly with the Strategic Direction – Asset Management:
- WG A1.33 has developed a guide for the proper storage and cleanliness of turbo-generators and their components. Strategic spares holding, operational units and ‘mothballed’ or temporarily inoperative equipment are high value assets and yet they can be relatively easily damaged by improper storage conditions or lack of attention to cleanliness control. The guide gives insight into good industry practice for the storage conditions, environmental control, type and frequency of testing/monitoring and cleanliness procedures put in place during the various storage and assembly periods to ensure a successful preservation of the equipment. A tutorial on this topic was presented at the SC-A1 meeting in India in 2019. The final version of the guide will be published in 2021.
- The concept and design of a hydro generator aims to achieve a machine that maximizes the value seen from the perspective of the customer while at the same time allows the manufacturer to innovate, optimize their design and provide current state of art in generator manufacture. The starting point is the technical equipment specification, and if it is not properly developed, the design resulting from it will not achieve the objective of optimal value for both the customer and manufacturer. WG A1.42 seeks to achieve consensus between customer and supplier so that the requirements contained in the technical specification are not a mere continuation of practices originated in the past or even impractical requirements due to a lack of equipment knowledge but to incorporate the current state of the art in the field. This work is nearing completion and the final report will be released in 2021.
- WG A1.55 is carrying out a survey on split core stators: Site access limitations and the significant size of large hydro generators can make it impossible to transport them as integral units and make site installation very difficult. A split core stator is a practical compromise. The design of a split core stator is more critical than a single continuous stator core as a poor design can result in core vibrations, noise or shaft voltage and can even lead to core and/or winding damage, shortening the stator life. It is therefore imperative to investigate and summarize the state-of-the-art designs, manufacturing, transportation and installation of split core stators as it will add significant value to engineering applications in the hydro-generator market.
- A survey on lap and wave windings and their consequences on maintenance and performance of hydro-generator stator windings has been carried out by WG A1.56. Specific design differences between lap and wave winding can affect manufacturing and installation costs as well as life cycle costs. In some cases, material savings and installation time reduction can be obtained using wave windings depending on the pole number, slot number and number of parallel current circuits. The focus of this WG has been to describe the different characteristics of lap and wave windings and give a guideline for the optimal choice. This work is also nearing completion and the final report will be released in 2021.
- When a stator winding fault to ground occurs in service on a hydro-generator it is not always possible to immediately replace the faulted coil due to operational, commercial or contractual reasons where the generator must be returned to service as soon as possible. The replacement of form-wound bars can be quite easy to perform with skilled personnel if spare bars are available. The situation is quite different when replacement of a multi-turn coil is required. The solution is often to cut out the faulted coil and to operate the generator with a voltage unbalance until a scheduled outage period in which the faulted coil can be replaced. WG A1.59 has evaluated different techniques and solutions for repairing failed stator windings and the work will be reported in 2021.
- WG A1.60 - Guide on economic evaluation for refurbishment or replacement decisions on hydro generators aims to develop guidelines and qualifying criteria in assisting Asset Management in the decision-making process regarding hydro generator refurbishment or replacement. It will complement the guide for turbo-generators described in Technical Brochure 641.
- WG A1.62 - investigates various problems, root cause analysis and operational limits on these types of bearings. Except for very small machines, the thrust bearings of hydroelectric units are hydrodynamic oil film tilting pad bearings. The utilization of a fluid film has several advantages such as low friction and almost no wear during continuous operation, the ability to remove the friction losses, and good damping. Even though oil has higher viscosity than, for example, water, the fluid film is very small in relation to the machines’ dimensions. Design features such as hydraulic or spring supports of the pads, which allow uniform load distribution and tilting, serve to maintain a stable oil film. White metal or plastic coatings on the pad improve the sliding in temporary absence of a fluid film and are enough to avoid wear or destruction of the parts. Such a component combines a multitude of physical effects such as fluid dynamics, tribology, heat conduction, heat convection, and solid body mechanics including thermo-mechanics. Failures in the design of these complex systems may lead to failures causing major outages.
- A large industrial plant may have more than a hundred motors. In power stations a motor failure may lead to difficulties in electricity generation or even lead to complete failure of generation. Decisions to repair or replace a failed motor should be based on variables such as: the original stator and rotor must be in reasonably repairable conditions, a thorough evaluation of the root-cause of the failure, repair cost, motor power rating and efficiency, load duty, environmental conditions, load factor, energy efficient motor purchase price, annual operating hours, electricity price, and economic analysis. To assist with this decision making, WG A1.64 is developing a guide for evaluating the repair/replacement of standard efficiency motors.
- WG A1.67 is tasked with developing a basic guide on the main state-of-the -art methods applied around the world for end winding corona testing, experience regarding the techniques, the devices used and the test conditions and, finally, establish the limit values in determining that end winding corona test results are acceptable or not.
SD 2: Machine/System Interaction
The behaviour of generators directly influences the behaviour of the system to which it is connected and vice versa. It is essential to clearly understand the effect both systems have on each other to enable effective management of a stable grid as well as to ensure prolonged life of generating equipment.
This strategic direction complements the work of study committee C4 ‘Power system technical performance’, the focus of SC-A1 being the impact on such interaction on the rotating machine and the machine properties and behaviour defined by its design which influence the power system response and reliability.
Since system performance is determined by the output and behaviour other generation sources on the same grid, then this strategic direction also has some overlap with SD 3 ‘Renewable Generation’. Similarly, the operational flexibility required by modern grids can influence the demands put on auxiliary components e.g. large motors (strategic direction 4).
Currently there are 2 activities related to ‘Machine/System Interaction’, 1 of which is a Joint Working Group with Study Committee C4.
- JWG A1/C4.52 - As wind generation is becoming a significant component of the generation portfolio in many power systems, provision of frequency-active power control is increasingly required for this technology in many regions. This Joint Working Group between A1 and C4 will document the state-of-art in developing such capabilities for wind turbine generators, as well as the system technical performance aspects of such controls and the impact of such controls on equipment design and performance.
- WG A1.54 has studied the effects of increased plant operational flexibility requirements on large motors. In recent years operational flexibility has become crucial for the commercial success of power plants to facilitate both larger penetration of renewable energy and the associated commercial considerations of operating in peak demand periods and the variability of renewable energy sources.
Cyclic operation, including two-shifting, operating at minimum load, and fast ramp up/down have all become normal for many power plants; even from quite an early stage of plant life. Cycling operation will result in more starting and stopping of auxiliary drives and this can result in several mechanisms which lead to deterioration of electric motor components. Typical failures that have been attributed to cycled operation include material fatigue arising from torque stresses on rotors during starting and stopping, and high starting currents causing thermal and electromagnetic effects.
The work has been completed and the report will be released in 2021.
SD 3: Renewable Generation
As part of carbon emission reduction initiatives, many countries have adopted policies to increase the installed capacity of renewable generation to either supplement or replace existing thermal generation. Wind and solar have proven to be the most popular choices and have seen a huge deployment worldwide with many countries now claiming high percentages of renewable power penetration into their generation mix.
However, with the retirement of large fossil-fuelled plant, this has led to a significant reduction in system inertia which impacts network frequency control capability and the ability to ride through system abnormalities and faults. This has in turn resulted in a resurgence in the installation of synchronous condensers/compensators at strategic locations in power distribution networks and the conversion of existing generators whose MW power output is no longer required.
Study Committees A1 and C4 have formed a Joint Working Group (JWG) A1/C4.66 to prepare a guide on the assessment, specification and design of synchronous condensers for power systems with high levels of renewable generation. The main objective of this WG is to produce an application guide which power network owners/operators and other parties can use to help determine network needs and thereby specify synchronous condenser design requirements to successfully maintain network inertia and other aspects necessary for a reliable power generation and distribution network.
The specific aspect of the frequency/active power control of wind generation is being addressed by JWG A1/C4.52 aligned with SD 2 ‘Machine/System Interaction’.
SD 4: Motors
Power plants use motors extensively throughout the many diverse systems to drive compressors, fans and pumps, and many other equipment which are critical to successful and reliable power generation. Historically the Advisory Group focused on large motors with ratings above 800 kW and 1000 V for power stations, but the scope has been adapted to include smaller rating, high efficiency motors used for dispersed generation in consideration of their large potential for reducing the energy consumed within a power plant.
The significant energy saving potential that high efficiency motors can have on future power generation is detailed in SC-A1 Technical Brochures 724 and 729.
This strategic direction also considers the evolution of motor technology as applied in power generation, and the manufacturing and operational aspects of motors across their full lifecycle.
There are currently 5 active Working Groups addressing this strategic direction.
- WG A1.45 is compiling a guide for Determining the Health Index of Large Electric Motors. The guide will aid utilities in identifying the appropriate measurements that are necessary for statistical quantification of in-service failure risk for effectively planned predictive maintenance interventions. The guide aims to quantify the severity of known motor defects’ in order to link it the likelihood/probability of functional failure. To enable this, large electric motors need quantitative analysis of monitored data, which when normalised with the motor operational and environmental conditions, will indicate the severity of the defect in relation to the level of functional in-service failure risk exposure.
- WG A1.53 shall elaborate on the design requirements of three phase induction motors for variable frequency drive (VFD) applications including a user guide for retrofitting of existing installations.
VFDs are used for several applications in utilities and industry like induced draft fans, cooling tower fans, condensate extraction pumps, compressors, coal conveyors, coal feeders and ventilation system equipment. As the penetration of VFDs in industry and in power stations has increased, several motor failures have been reported worldwide and it has become clear that manufacturers do not have common design criteria for inverter grade motors considering the different stresses imposed on motor insulation by the variety of available VFD technologies. The WG is close to completion and the report is scheduled for release in 2021.
- WG A1.54 – Impact of Flexible Operation on Large Motors. The scope of this topic is shared with and described under Strategic Direction 2.
- In industrial applications, squirrel cage induction motors are widely used. The materials used for the manufacturing of the rotor cage can be from different conductive metals, with the most used ones being aluminium alloys and copper. With these materials, the cage of the rotor can be manufactured by die-casting or welding processes. Both materials have advantages and disadvantages, which are not always clearly understood. WG A1.58 aims to compile a guide for the selection of copper versus aluminium rotors for induction motors.
- WG A1.68 was established to compile a guide covering the best available practices on evaluating the quality performance of motor manufacturing and repair facilities.
SD 5: Machine Monitoring, Diagnosis and Prognosis
Condition Monitoring is a vital instrument in any business as it can result in significant cost savings if done correctly and effectively. The field of condition monitoring is one of continuous evolution and development. The long-term goal of any plant owner is to effectively operate machines to achieve maximal performance, reliability and efficiency and to make intelligent maintenance decisions through understanding the behaviour and signs of deterioration. The system can also be designed to provide diagnosis of machine condition allowing the prediction of problems, optimize operational efficiency and improve plant productivity.
The term ‘digital twin’ has been coined in recent years referring to a mathematical model that can be used to interpret and assess live data streamed from the power plant to centralised diagnostic centres. Further development in this field applied to rotating electrical machines is anticipated.
There are currently 9 active SC A1 groups performing work in this field. 4 are already well-established; 2 of which will release their reports in 2021. A further 5 WGs are in a relatively early phase.
- WG A1.43 focusses on state-of-the-art rotor temperature measurement systems. Unexpected failure of any component can result in forced outages and costly emergency repairs. Some rotating machines today are equipped with temperature measurement instrumentation to detect local overheating of rotor windings or, in the case of hydro-generators, rotor structure. This topic is of high importance, not just for machine monitoring and diagnostics purposes, but also for the purposes of machine design and construction improvements. The completed Technical Brochure for this work will be published in 2021.
- WG A1.44 is compiling a guideline on Testing of Turbo and Hydro-generators. Previously published TB 386 ‘Generator Maintenance, Inspection and Test Programs’ provided recommendations regarding maintenance, inspection and testing of turbo-generators in power plants. This guide will complement that work by providing guidance to plant personnel on test procedures and practices to ensure equipment integrity, including hydro-generators, as well as an overall guidance regarding safety precautions, industry references, acceptable ranges of results, and, where appropriate, actions to be taken should the results be outside acceptable ranges.
- WG A1.48 is working on guidance on the requirements for high speed balancing / over-speed testing of turbine generator rotors following maintenance or repair. The requirement for testing a generator rotor following maintenance varies substantially across the industry, with different methodologies being applied depending on the nature of the repair work, the owner/operator, the original equipment manufacturer (OEM) and the geographical location of the equipment. Figure 1 illustrates the logistic difficulties and delays in carrying out a rotor high speed balance if the power station is located in certain areas of the world. This guide intends to simplify the decision making of whether to carry out high speed balancing on generator rotors following repair work. The work has been completed and the Technical Brochure will be issued in 2021.
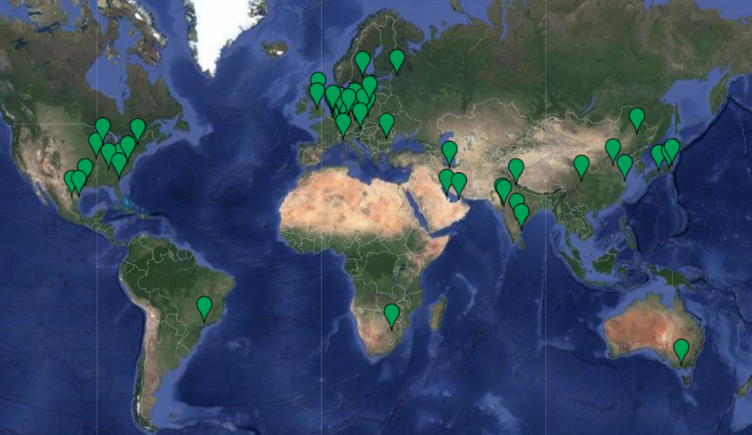
Figure 1 - Locations of high-speed testing facilities for generator rotors (>25 t)
- The predictive diagnosis of winding insulation in large motors (more than 800 kW and 1000 V) is of great importance, for both technical and economic reasons. In October 2004 SC A1 published the Technical Brochure: “Application of On-line Partial Discharge Tests to Rotating Machines”, providing guidance on where it is appropriate to apply partial discharge (PD) measurements and providing a proper focus on what results could be expected. Since then IEC/TS 60034-27, IEC/TS 60034-27-2, IEEE Std 1434 concerning the subject of PD measurements on the stator winding insulation of rotating machines have all been updated (in 2006, 2012 and 2014 respectively). The technologies in this field have evolved fast and new measurement and diagnostic tools are now available, including new kinds of PD sensors and new signal processing tools for noise and disturbance suppression. Simultaneously, the industrial use of converter fed high-voltage machines is steadily growing. Particularly in motors, where the effects of motor drivers on the insulation aging process and in PD monitoring have a significant influence, there is still a lack of information, reference cases and standard procedures. WG A1.61 - Survey of Partial Discharge Monitoring in Large Motors is tasked with filling this information gap.
- 4 newly established WGs relate to hydro-generators. WG A1.69 addresses measured v calculated excitation current anomalies, whilst WG A1.71 and A1.72 will carry out surveys on rotor damper winding concepts, and multi-turn stator coil construction respectively. WG A1.73 will assess customer requirements for the qualification of form wound stator insulation systems for hydro-generators.
- WG A1.70 will build on the excellent work done on the use of Dielectric Dissipation Factor (DDF) measurements in relation to the assessment of the condition and quality of stator insulation systems of rotating electrical machines (reported in Technical Brochure 769) by focussing on DDF measurements of complete stator windings.
SD 6: Efficiency of Electrical Machines
Generators and motors are the highest efficient components used in the power generation process, with power conversion efficiencies ranging from 98% to 99%. Further improvement on these efficiencies has proven possible, but requires highly advanced modelling requiring complex algorithms, making use of all technical knowledge and experience available, pushing technologies to its absolute safe limits. On a large turbo generator of 1000MWe output, a 0.1% improvement in efficiency can result 1MWe extra being available to the national grid, powering an additional 50 to 60 households, without any increase to operational costs.
Traditionally efficiency increase has focussed on base load operation and the development and application of advanced calculation tools and new materials has been used to improve cooling and electrical insulation heat transfer characteristics in both generators and motors, thereby directly contributing to the increase in efficiency of these electrical machines. However, with a gradual change in the load duties of large power plant in support of the increasing penetration of renewable power sources, machines will operate more and more at part loads for relatively short and variable time frames. Rotating machines are generally optimised at the design rating so operation at part load results in a decrease in the actual mean efficiency that can be achieved. An adaptation of the cooling or other operating parameters according to the load is more likely to be in focus in future.
Currently however there are no active working Groups on this topic.
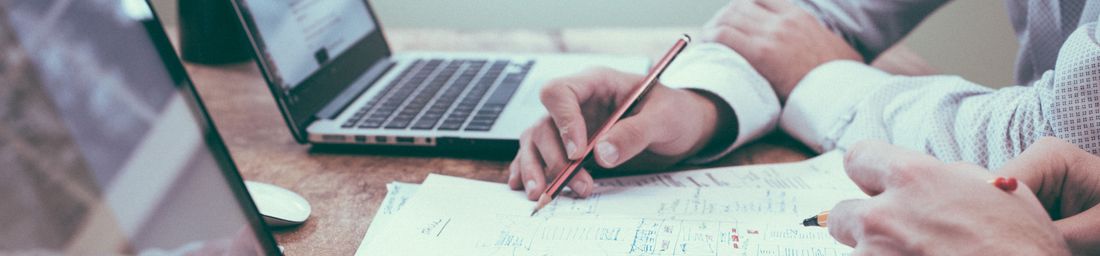
CIGRE active Working Groups / Call for experts
SC A1 2020 e-Session
Due to the prevailing COVID situation, the 2020 session took place in the form of an e-Session. The Study Committee A1 sessions were held on Tuesday 25th and Wednesday 26th of August. The e-Sessions consisted of two paper presentations held on each of the two days and one tutorial held on Tuesday after Paper Session 1. The number of attendees varied between 93-103 for session 1, and 57-69 for session 2 over the 4-hour durations.
The Study Committee meeting took place on Friday 29th August 2020. This was the last meeting chaired by Nico Smit who has done an excellent job in guiding SC A1 over the last 6 years. He has thoroughly deserved the honorary membership he received from CIGRE for his hard work and dedication.
Thanks to the engagement and preparation of the presenters and SC A1 team, and the active participation of the attendees, it was a great and successful achievement considering the circumstances with attendee levels equalling that typically achieved at the Paris Sessions. The Q&A sessions were both interesting and informative.
The papers and discussions covered the following Preferential Subjects:
- Preferential Subject 1: Generation Mix of the Future
- Preferential Subject 2: – Asset Management of Electrical Machines
- Preferential Subject 3: – Developments of Rotating Electrical Machines and Operational Experience
The Paper Session 1 held on Tuesday morning was divided up into three sessions of video presentations. The three sessions covered the following topics:
- Synchronous Compensators (PS1 & PS3 - 6 Papers)
- Partial Discharge (PS2 - 5 Papers)
- Condition Monitoring (PS2 - 3 papers)
The Paper Session 2 held on Wednesday morning was divided up into three sessions of video presentations. The three sessions covered the following topics:
- Design Optimisation (PS2 & PS3 - 5 Papers)
- Operational Optimisation (PS2 & PS3 - 4 Papers)
- Standards (PS2 & PS3 - 4 Papers)
The next Study Committee Meeting will take place in Paris, France on the 26th of August 2021. The Preferential Subjects for the meeting in Paris will be as for 2020 and the Group Discussion will be based on the Special Report to be released in 2021:
PS 1: Generation Mix of the Future
- Effect and risk of an increasing renewable power mix on existing legacy generators, generator auxiliaries, and motors
- Improvement in designs and maintenance practices to comply with new and future grid requirements
- Evolution and trends in new machines for renewable generation
PS 2: Asset Management of Electrical Machines
- Experience with refurbishment, replacement, design improvements, power up-rating, and efficiency improvement of aged generators and motors
- Optimised condition monitoring, diagnosis, prognosis, and maintenance practices to improve reliability and extend operational life
- Operational and project experience: installations, failure analysis; robotic inspections; recovery options; cost and time reduction initiatives; and effects of torsional electromechanical oscillations for synchronous compensators, wind turbine generators, turbo-generators, hydro-generators, and motors
PS 3: Latest Developments
- Designs, specifications, materials, manufacturing, maintenance, performance, and efficiency improvement of electrical machines
- Condition monitoring techniques and equipment
2020 Awards
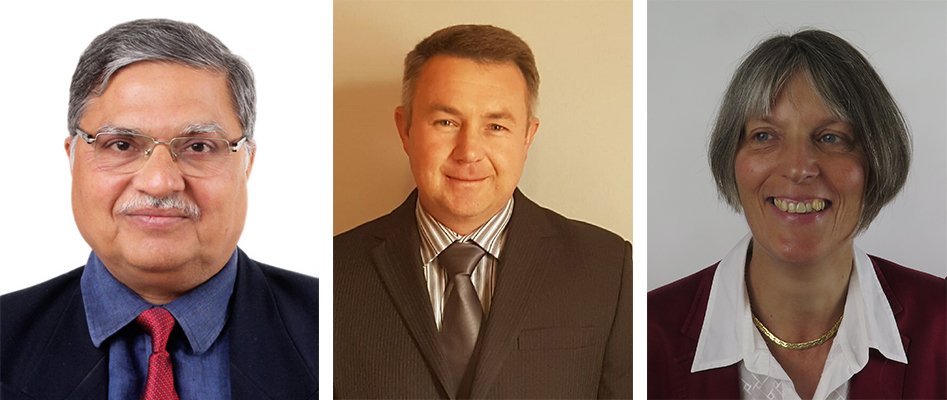
In 2020 three SC A1 members received awards for their outstanding contributions to the work of the Study Committee over several years. Congratulations on these well-deserved acknowledgments.
From left to right : D.K. Chaturvedi, CIGRE Fellow, Nico Smit, Honorary Member, Former Chair of SC A1, and Monique Krieg-Wezelenburg, 2020 Technical Council Award
Tutorials
Tutorials are regarded as a valuable initiative to disseminate knowledge gained from the work done by Working Groups within the Study Committee. One tutorial was delivered by SCA1 during the SCA1 2020 e-Session:
"Specification vs Value of New Hydro-Generators – A Cause and Consequence Trade-Off" was presented by Mr Johnny Rocha on Tuesday afternoon following the Paper Session 1.
Future activities
Future activities are guided by the strategic directions defined within the Study Committee. These are regularly reviewed to ensure they remain relevant to current and foreseen trends in the application of rotating electrical machines in power generation.
A current recurring theme is the role of large machines in supporting grid reliability in the face of power fluctuations and unpredictability from renewable generation sources. The focus on new plant is not only the power output but the potential contribution to system inertia, short circuit power and the ability to ride through grid disturbances. The increased demand on the flexibility of operation of both new and existing plant, e.g. rate of change of frequency (ROCOF) is presenting real challenges to the application of standard designs.
Fossil fuelled plant has seen a general out-phasing and replacement by wind and solar generation in many countries. However, some plant has needed to be retained as back-up for fluctuations in the renewable power supply, whilst other plant is being converted to synchronous compensator duty to ensure system stability. The extended use of existing plant in this way together with the changing commercial considerations of revenue for intermittent duty/availability and MVAr compensation make asset management, combined with monitoring and maintenance strategies, critical aspects of power generation planning.
The high level of introduction of wind turbines over the last few years across the world has meant that there is a huge installed base that is developing quickly both on- and off-shore. Whilst initial unit sizes were small, they have increased steadily and today have reached 10 MW for the latest offshore applications and which are planned for large scale wind farm installation. This again raises the topics of monitoring, reliability, availability and maintenance strategies of wind generators in locations with limited access, availability of suitable equipment, and weather constraints on the timing of maintenance activities.
Study Committee A1 will need to be active in all of these areas to continue to bring benefit to its members.
If you have any comments or suggestions or would like to know more about the activities of Study Committee A1, please do not hesitate to contact the Chair or Secretary.
Currently Active Working Groups
One Working Group was disbanded in 2020, after completion of their activities, with publication of a Technical Brochure and Electra Report. 5 new WGs were approved in 2020 and have either started work or are in the course of building the team. Unfortunately, 3 WGs had to be cancelled due to difficulties in completing the work as originally defined; where appropriate some of these will be reconsidered and adapted for future. 1 WG is paused awaiting appointment of a new convener.
Table 1 lists the 26 active Working Groups in the Study Committee. Of these, 3 are awaiting publication, and 5 are nearing completion. The focus of the first half of SC-A1 activities will be to complete and publish these 8 reports; proposals for further Working Groups will be reviewed during the 2021 CIGRE Session planned to take place in Paris.
WG # | Title of the Working Group | Convener |
---|---|---|
A1.44 | Guideline on Testing of Turbo and Hydrogenerators | Mladen Sasic |
A1.45 | Guide for Determining the Health Index of Large Electric Motors | Dr. Zhang Pinjia |
A1.52 | Wind generators and frequency-active power control of power systems | Nicholas Miller |
A1.55 | Survey on Split Core Stators | Sun Yutian |
A1.58 | Selection of Copper Versus Aluminium Rotors for Induction Motors | Fredemar Rüncos |
A1.60 | Guide on economic evaluation for refurbishment or replacement decisions on hydro generators | Mark Bruintjies |
A1.61 | Survey of Partial Discharge Monitoring in Large Motors | André Tomaz de Carvalho |
A1.62 | Thrust Bearings for Hydropower - A Survey of Known Problems and Root Causes | Daniel Langmayr |
A1.63 | Turbo Generator Stator Winding Bushings and Lead Connections – Field Experience, Failures and Design Improvements | To be appointed |
A1.64 | Guide for Evaluating the Repair/Replacement of Standard Efficiency Motors | Erli Ferreira Figueiredo |
A1.66 | Guide on the Assessment, Specification and Design of Synchronous Condensers for Power Systems with Predominance of Low or Zero Inertia Generators | D.K. Chaturvedi |
A1.67 | State of the Art in methods, experience and limits in end winding corona testing for Hydro Generators | Hélio de Paiva Amorim Junior |
A1.68 | Evaluating Quality Performance of Electric Motor Manufacturing and Repair Facilities | Kondra Nagesh |
A1.69 | Hydro-Generator Excitation Current Anomalies | J. Johnny Rocha E. |
A1.70 | Dielectric Dissipation Factor Measurements on Stator Windings | Monique Krieg-Wezelenburg |
A1.71 | Title of the Group: Survey on damper-winding Concepts and its operational experience on hydro generators and motor-generators | Thomas Hildinger |
A1.72 | Survey on multi-turn coils with dedicated turn insulation versus coils without dedicated turn insulation | Yoon Duk Seol |
A1.73 | Customer Requirements for Qualification of Form Wound Stator Insulation Systems for Hydro Generators | Franz Ramsauer |
Publications
One Technical Brochure was published in 2020 and, with three more Working Groups nearing completion, the total number of reports planned for 2021 increases to eight.
SC A1 Technical Brochures planned for in 2021
A1.33 | Guide for Cleanliness and Proper Storage of Generators and Components |
---|---|
A1.43 | State of the Art of Rotor Temperature Measurement |
A1.48 | Guidance on the Requirements for High Speed Balancing / Over-speed Testing of Turbine Generator Rotors Following Maintenance or Repair |
A1.42 | Influence of Key Requirements to Optimize the Value of Hydro Generators |
A1.53 | Guide on Design Requirements of Motors for Variable Speed Drive Application |
A1.54 | Impact of Flexible Operation on Large Motors |
A1.56 | Survey on Lap and Wave Winding and their Consequences on Maintenance and Performance |
A1.59 | Survey on Industry Practices and Effects associated with the Cutting Out of Stator Coils in Hydrogenerators |
This table lists all publications released by SC A1 since 2003 for reference. They are available for download on the e-cigre website.
TB N° | Technical Brochure name |
---|---|
813 | Magnetic core dimensioning limits in hydro generators |
776 | Factory Quality Assurance Testing Requirements for Turbo-Generator Components - Stator Bars |
774 | State of the Art of Stator Winding Supports in Slot Area and Winding Overhang of Hydro Generators |
772 | Turbo-generator stator windings support system experience |
769 | Dielectric Dissipation Factor Measurements on New Stator Bars and Coils |
743 | Guide on New Generator Grid Interaction Requirements |
729 | Technological Feasibility Studies for Super and Ultra-Premium Efficient Motors |
724 | Guide on Use of Premium Efficiency IE3motors for Determining Benefits of Greenhouse Gas Emission Reduction |
690 | Vibration and Stability Problems met in New, Old and Refurbished Hydro Generators, Root Causes and Consequences |
682 | Survey on Hydro Generator Instrumentation and Monitoring |
665 | Hydro-generator Behaviour Under Transient Conditions |
641 | Guide on Economic Evaluation of Refurbishment / Replacement decisions on Turbo-generators |
621 | Generator On-Line Over and Under Excitation Issues |
582 | Survey on Hydro Generator Cleaning |
581 | Guide - Corona Electromagnetic Probe Tests (TVA) |
574 | Guide for Consideration of Duty on Windings of Generators |
573 | Guide for Minimizing the Damage from Stator Winding Ground Faults on Hydro-generators |
558 | Guide for the Monitoring, Diagnosis and Prognosis of Large Motors |
552 | Guide of methods for determining the condition of stator winding insulation and their effectiveness in large motors |
551 | Feasibility of Updating from Class 155 (F) to Class 180 (H) the Electrical Insulation Systems in Electrical Rotating Machines |
522 | Generator Stator Winding Stress Grading Coating Problem |
517 | Guide for the Prevention of Over-fluxing of Generators |
503 | State of the Art and Capacity for Robotic Inspection of Turbo-generators |
491 | Generator End-Winding Retaining Rings – A Literature Survey and Care Guideline |
480 | Guide on Stator Water Chemistry Management |
470 | Life Extension of Large Electric Motors in Nuclear Power Plants |
469 | State of the Art in Efficiency of Hydro Generators Commissioned since 1990 |
454A | Hydro-generators Fire Protection – Update (Annex) |
454 | Hydro-generators Fire Protection – Update |
437 | Guide for On-Line Monitoring of Turbo-Generators |
397 | Guide for minimizing the damage from stator winding grounds on Turbo-generators |
392 | Survey of Hydro-generator Failures |
386 | Generator Maintenance, Inspection and Test Programmes |
258 | Application of On-Line Partial Discharge Tests to Rotating Machines |
257 | EL CID Testing of Large Steam-Turbine-Driven Generators |