Application of robotics in substations
The application of robots could improve personal safety, enhance operation and maintenance efficiency, and provide comprehensive information for asset management. This TB provides an overview of the existing applications of robotics in substations for construction, inspection, maintenance, and operation. It also presents the current and expected future trends in the development of new robot systems, pointing to the need for further research and standardization.
Convenor
(CN)
J. FAN
Secretary
(US)
S. SAGARELI
L. LI (CN), T. SUGIMOTO (JP), R. ISHINO (JP), S. MONTAMBAULT (CA), A. RENTON (NZ), J. BEAUDRY (CA), P. PATEL (US), M.M. GONZALEZ (ES), X. JI (CN), R. GUO (CN)
Corresponding Members: G. MOTA (PT), A. SHAH (US), J.F. ALLAN (CA), Y. LI (AU)
Introduction
Traditional life-cycle management of substations requires significant manpower and is typically hindered by issues pertaining to efficiency, consistency, quality, and safety (especially in high voltage environments), which can be further compromised by severe climate conditions and at difficult to access locations. Substation owners, asset managers, and engineers are always looking for ways to achieve highest levels of safety and minimizing the costs of substation construction, operations, and maintenance. These goals can be achieved by employing robots. Rapid advancements in artificial intelligence and sensor technologies lead to development of robotics, which could replace or assist people in substation operations and management. Some of these robots are already used in substations, with excellent results.
This Technical Brochure (TB) provides an overview of the existing applications of robotics in substations. It also presents the current and future trends in the development of new robot systems.
Scope and Methodology
To gain a thorough understanding of the current state of research on substation robots and their applications, and thus promote the effective application in substations, the Working Group (WG) B3.47 was set up in November 2016 and was tasked with the following responsibilities:
- Investigate and research worldwide requirements for the application of robotics in substations;
- Define main application scenarios;
- Identify key technical requirements and challenges;
- Conduct case studies describing best practices;
- Identify standardization requirements and provide suggestions for the follow-up work.
In order to get more information, a survey was designed for utilities and research institutes & manufacturers, mainly covering application scenarios, functional requirements, key technologies, current applications, and standardization requirements. The survey was conducted in 15 countries, focusing on those where substation robotics research is most advanced.
Description of TB
Historical overview
Historical overview of the developments in the field of robotics in general, and in substation robotics is provided in Chapter 1.
Survey and categories of robotics in substations
Chapter 2 presents results of the questionnaire that consisted of 54 questions, mainly covering application scenarios, functional requirements, key technologies, current applications, and standardization requirements. Based on the survey statistical data, we could find the current application situation, functions and key technologies of existing substation robots, technological demands and development trends.
To facilitate better understanding of robotics, a definition of substation robots was proposed, based on the survey findings and analyses of the robotic systems presently used in substations. Classifications based on different criteria are presented to show the technical features that distinguish different robot types. See Figure 1.
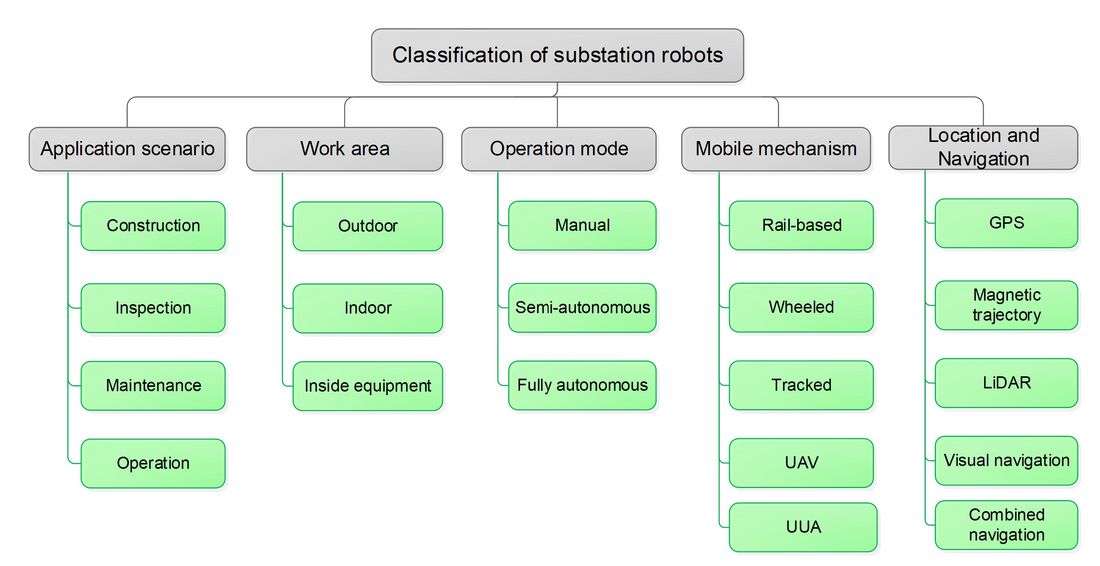
Figure 1 - Classification of substation robots
Substation construction robots
Chapter 3 is designated for in-depth examination of existing and emerging substation construction robots, as well as their key functions and technologies, benefits and challenges.
Construction using robotics requires precise three-dimensional data. As a result, after the construction work is finished, three-dimensional data is obtained as a by-product. Three-dimensional data is useful for maintenance, planning and design when managing facilities and planning the replacement of facilities. Therefore, it is essential to be aware of the state of development of unmanned construction methods using robotics.
Robots often carry out tedious and simple tasks. For example, a robot can be used for treating concrete walls and another for binding steel reinforcement rods.
Substation inspection robots
Chapter 4 is dedicated to inspection and patrol robots, including general architecture of robotic systems, current functionalities, and key technologies used in inspection robots.
In ten years of recent technology improvement, UGV-based patrol robots have been developed and deployed in outdoor substations. Robots now utilize GPS localization and 2D laser localization, which considerably extends their navigation capabilities. Moreover, their inspection scope has been extended from visible-light and infrared monitoring to partial discharge detection based on ultrasonic and transient earth voltage detection. Thus far, over 1,000 outdoor patrol robots have been put into full operation worldwide
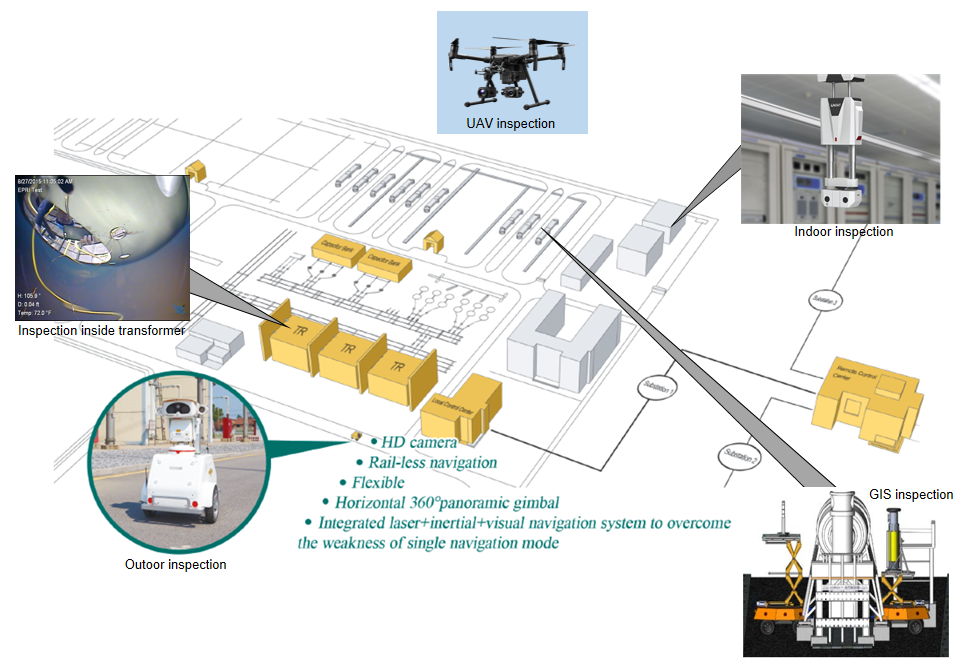
Figure 2 - Overview of exiting substation inspection robots
Substation operation robots
Many other types of inspection robots have been developed in the last decade, as well, such as indoor rail-mounted patrol robots, valve hall patrol robots, PD inspection robots, and transformer internal inspection robots – see Figure 2.
Many of these robots are capable of self-localization and fully autonomous navigation within substations, which makes them suited for autonomous patrol or inspection, as appropriate.
Substation maintenance robots
In Chapter 5, maintenance robots are discussed, including those employed for live washing and cleaning and other substation maintenance tasks. System composition, functions, performance, benefits, and challenges of live line working robots are also presented.
A live maintenance robot has been used to complete the post insulator cleaning, dry ice blasting, removal of foreign objects, repair of broken conductors, and other live work.
Substation operation robots
Chapter 6 provides information on existing and emerging operation robotics, such as breaker racking robots and robots capable of performing switching operations in remote unattended substations. Certain firefighting robot systems are also introduced.
A circuit breaker racking robot prototype has been tested, which could lift breakers exceeding 400 kg in the switchgear room by being manually driven in the control room. The robot can be commanded to automatically align with and pick up a breaker from the floor. A tele-operated patrol robot with a robotic arm has been developed to carry out visible and infrared inspection of substation equipment under a snow cover at -30 °C and operate a disconnect switch and other substation equipment by means of a mechanical arm.
A prototype of an intelligent firefighting robot can operate in extremely high temperatures, as well as in toxic and anoxic environments affected by heavy smoke, to substitute manual firefighting operations. Firefighting robot systems for large-scale facilities consist of flying type reconnaissance & surveillance robots, ground reconnaissance & surveillance robots, water cannon robots, hose extension equipment, and command systems, all of which is transported in one vehicle. Figure 3 shows a conceptual image of their operation.
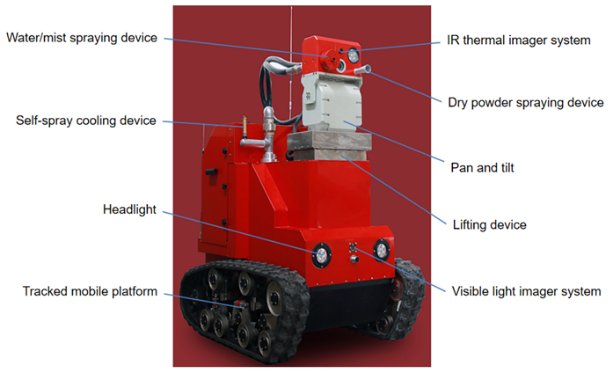
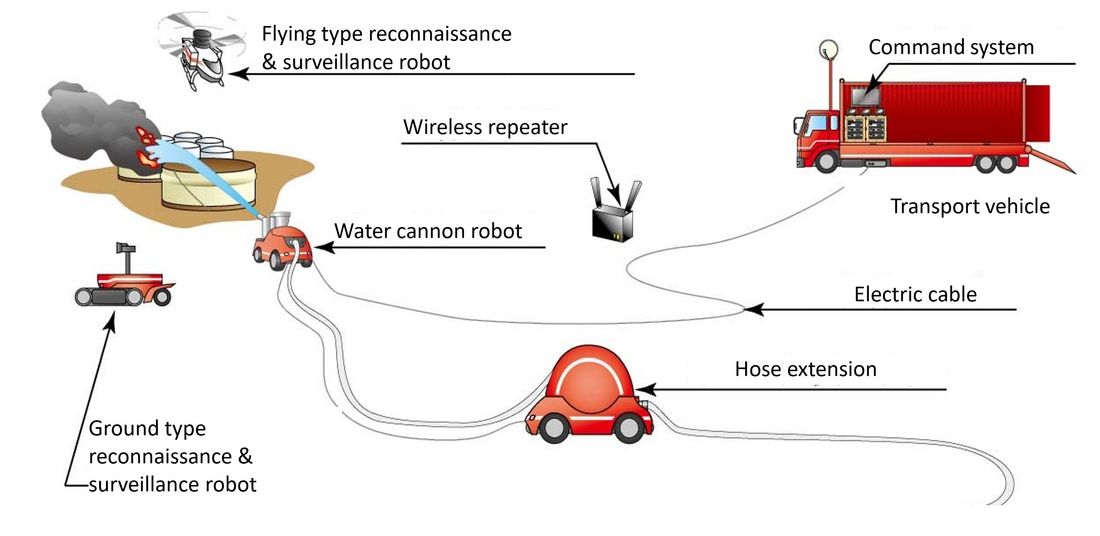
Figure 3 - Firefighting robot systems
Left: A firefighting robot protype / Right: A firefighting robot system for large-scale facilities
Standardization analysis
Chapter 7 provides specific references to relevant IEC, ISO, IEEE, etc. standards, followed by national standards adopted in several countries. Based on these findings, a standard system framework for robotics applied in substations is proposed, as shown in Figure 4.
The standards for robots used in substations may include some general standards, in addition to those for individual robots of various types. Based on the lifecycle of robots, standards can be formulated to include requirements on system design, functions and performance, testing, commissioning and acceptance, operation and maintenance, as well as discarding and recycling. Priority should be given to standardization for robots with proven technology and clear user requirements, such as patrol robot systems used outdoors, to aid in more widespread application of such robots on a global scale.
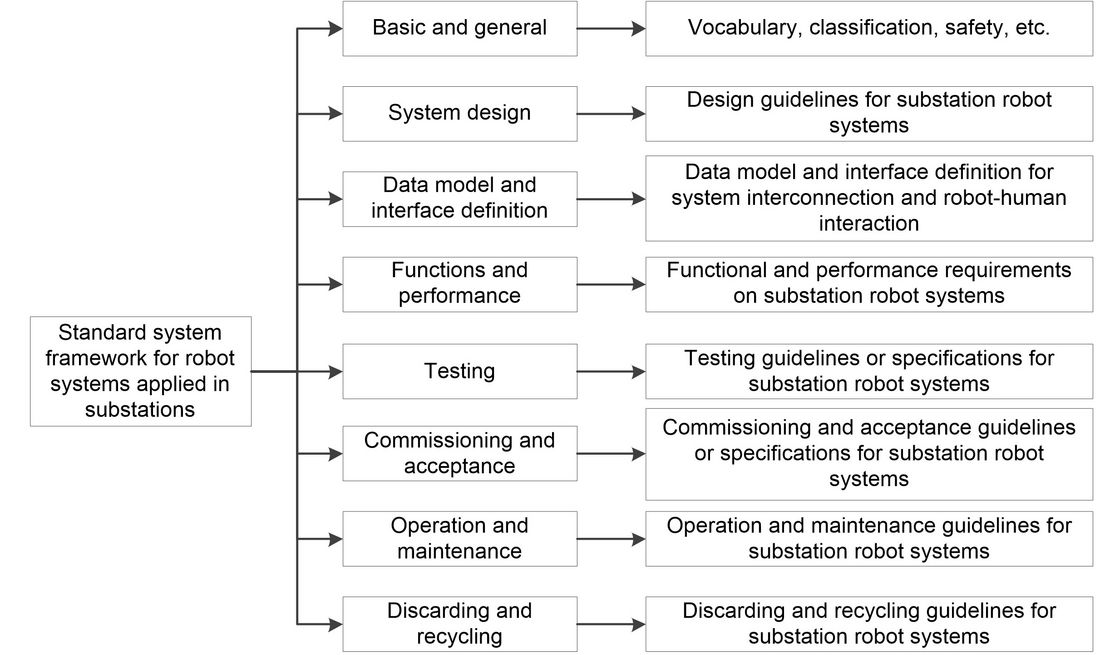
Figure 4 - Standard system framework for substation robot systems
Conclusion
Readers of this TB will gain a comprehensive understanding of the current state of the art and research on substation robots and their applications. Benefits, development trends, and proposals for standardization of substation robots are analyzed and presented.
Robotics for substation being currently used and developed, include full spectrum of applications that cover whole lifecycle of substation from design to construction to inspections, operations and maintenance. In construction, their functionalities include taking measurements, 3D scanning, design, construction, and inspection, as these are the main activities targeted for automation in countries facing labor shortages and population aging. Substation inspection robots have been put into full operation for patrol and inspection equipment in outdoor and indoor environments, as well as in valve halls and inside the transformers. GIS inspection robots are being developed, and UAV-based inspection systems are presently being tested. Prototypes of robots performing water washing, dry ice blasting, brush cleaning, and replacement of drop-out fuses have been built and tested. Robots for autonomous breaker racking and disconnect switch operations are designed to eliminate the need for direct contact between humans and equipment. Firefighting robots are developed to minimize hazards and losses caused by fire.
The benefits of application of substation robots include improving personal safety, enhancing operation and maintenance efficiency, and providing information for asset management. Deployment of robots in substations also provides an effective solution to the problems pertaining to safety, labor shortages, workplace hazards, and unattended operation.
To improve product and service quality and promote global application of substation robots, international consensus standards should be developed through the IEC ISO, IEEE, etc. They should cover technical requirements for robot systems, and interfaces between robots and utilities’ infrastructure. This will ensure more reliable services, eliminate repeated development, lower the initial and maintenance costs.